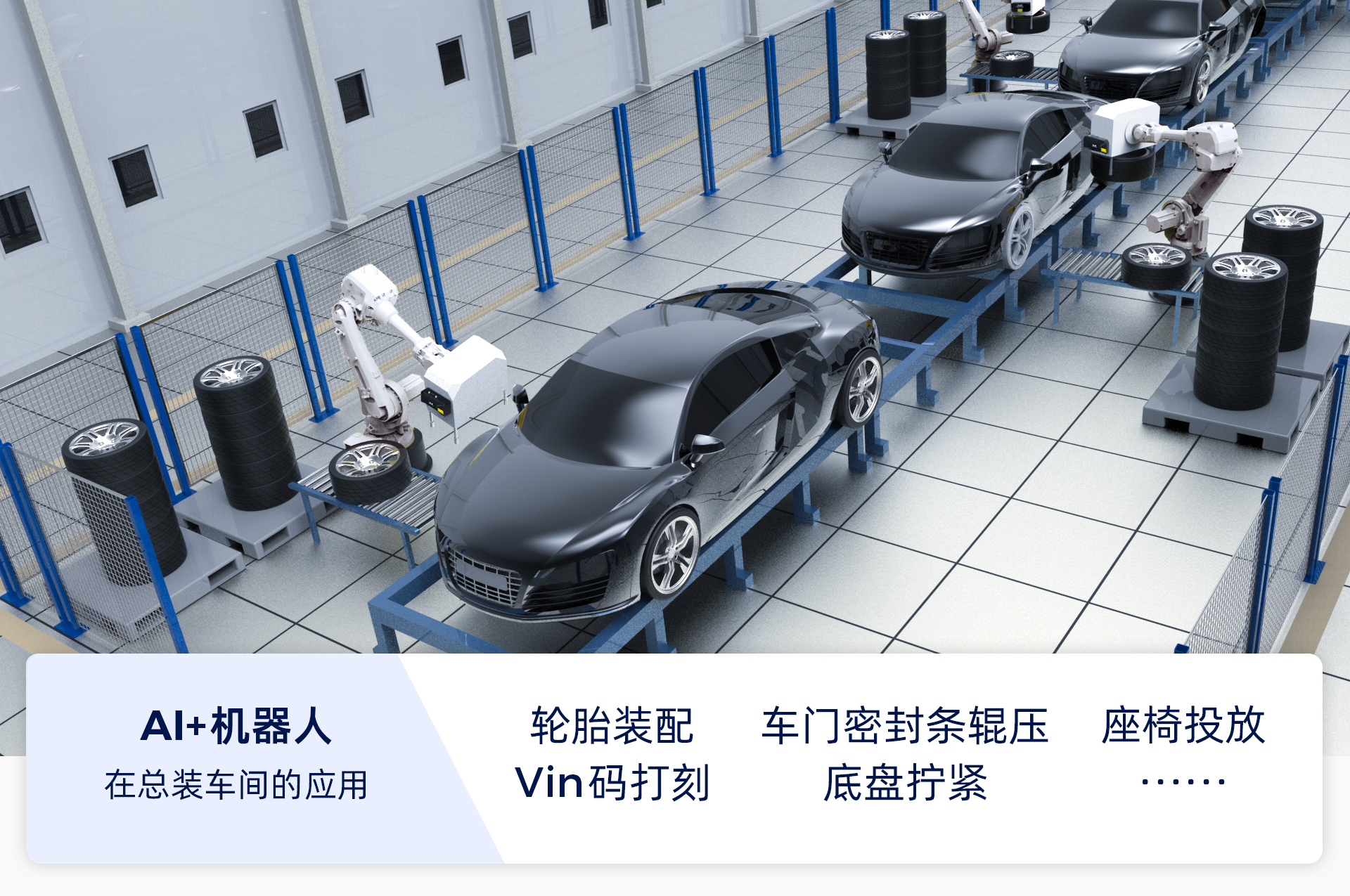
-
在总装车间,各类分总成和零部件被组装成一辆完整的汽车。这一车间的效率、精度、生产稳定性等因素,直接决定了汽车的质量、安全性能及交付周期。然而,总装车间工艺流程复杂、技术指标要求高、需支持多车型混线生产,传统的人工操作结合机械辅助的方式已难以满足车企日益增长的发展需求。
针对总装车间的复杂挑战,梅卡曼德为汽车主机厂提供了性能强大、柔性易用的AI+机器人产品,已在多家汽车制造头部企业的智能工厂中实现批量化部署,包括Vin码打刻、仪表台安装、座椅投放、玻璃安装、密封条辊压、底盘拧紧、轮胎随行装配等典型应用场景。通过提升质量标准、生产效率、柔性化生产能力及缩短交付周期,梅卡曼德为车企提供了强有力的技术支持,助力汽车制造向智能化、自动化方向持续迈进。

内饰一线装配:基础内饰件的装配,如仪表台、线束、密封条等部件的装配。
内饰二线装配:功能性内饰件的装配,如座椅、车门等的装配。
分装作业:在多个分装线上同步进行关键模块的预装,如:车门分装、仪表台分装、底盘分装等。
底盘总装:将动力总成、悬架、转向系统等安装到底盘托架上。
车身合装:将底盘总成、车轮等分装模块与车身进行合装,完成整车的基本结构装配。
1.车身导入:AI+机器人进行Vin码打刻
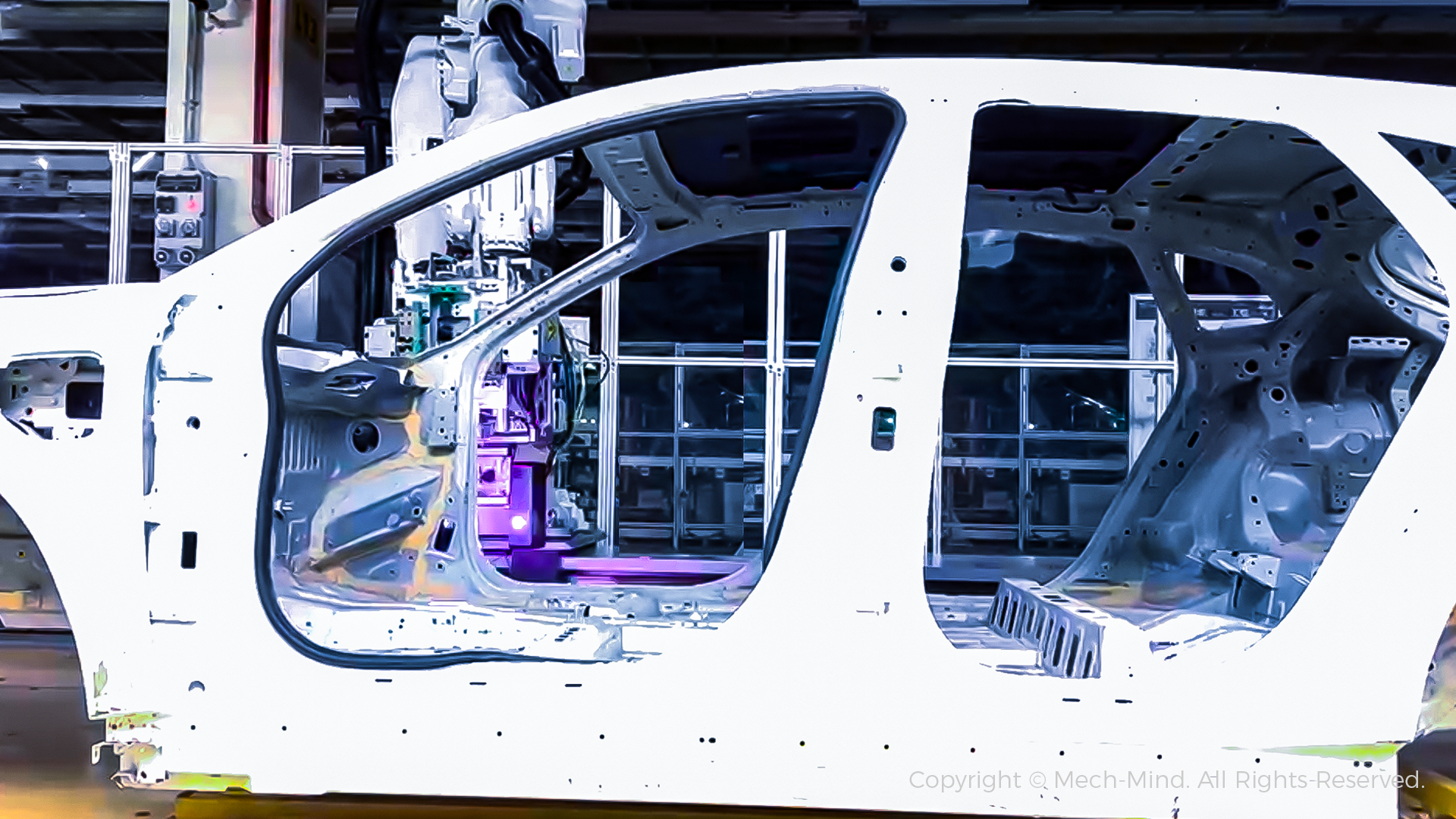
应用背景:
Vin码(车辆识别码)是车辆身份识别和质量追溯的重要标识。传统Vin码打刻通常由操作人员手动定位打刻位置,再使用打刻机完成打刻。这种打刻方式通常存在打刻速度慢、精度低、一致性差等问题。车身到位位置存在偏差,3D视觉先对车身前门进行定位,确保机器人携打刻机顺利进入前车舱;随后,3D视觉再对车底Vin码打刻位置进行精确定位,引导机器人携打刻机完成高精度打刻。
3D相机结构设计紧凑,支持臂载式安装,灵活适应复杂的车身结构。
AI+机器人柔性适配能力强,能够快速适配不同车型的打刻需求,支持多车型混线生产。
Vin码打刻精度及一致性大幅提高,打刻速度满足产线高节拍生产要求。
2.内饰线:AI+机器人进行仪表台涂胶及安装
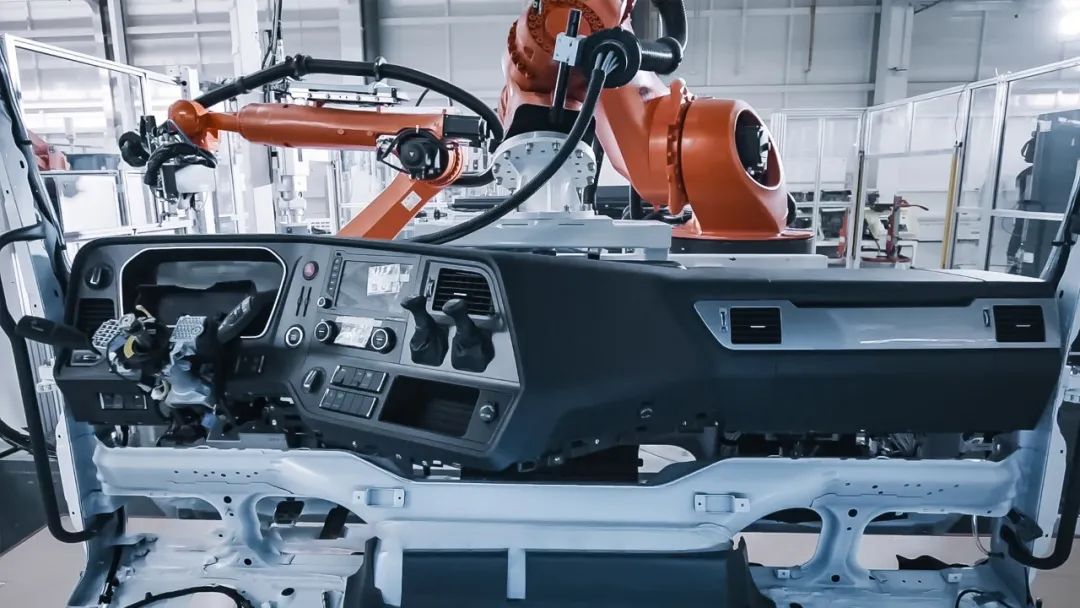
应用背景:
仪表台是重要的汽车内饰件,其装配质量对于汽车驾驶体验及安全性都有着重要影响。传统工艺中,采用人工搬运+机器人示教的方式进行涂胶及安装,存在效率低、精度差、一致性差等问题。应用优势:
3D视觉分别引导装配机器人及涂胶机器人抓取仪表台并定位涂胶位置,涂胶机器人施胶。随后,3D视觉定位前车舱,引导装配机器人将仪表台精准安装于驾驶室。
先进成像算法,能够对黑色仪表台及高亮反光的车身骨架生成高质量点云数据。
AI算法能够快速适配不同车型仪表台的安装需求,实现多车型柔性化生产。
通过机器人技术和AI+3D视觉相结合,完成大重量、大尺寸仪表台的搬运、涂胶和高精度装配,确保了装配质量的一致性和稳定性。
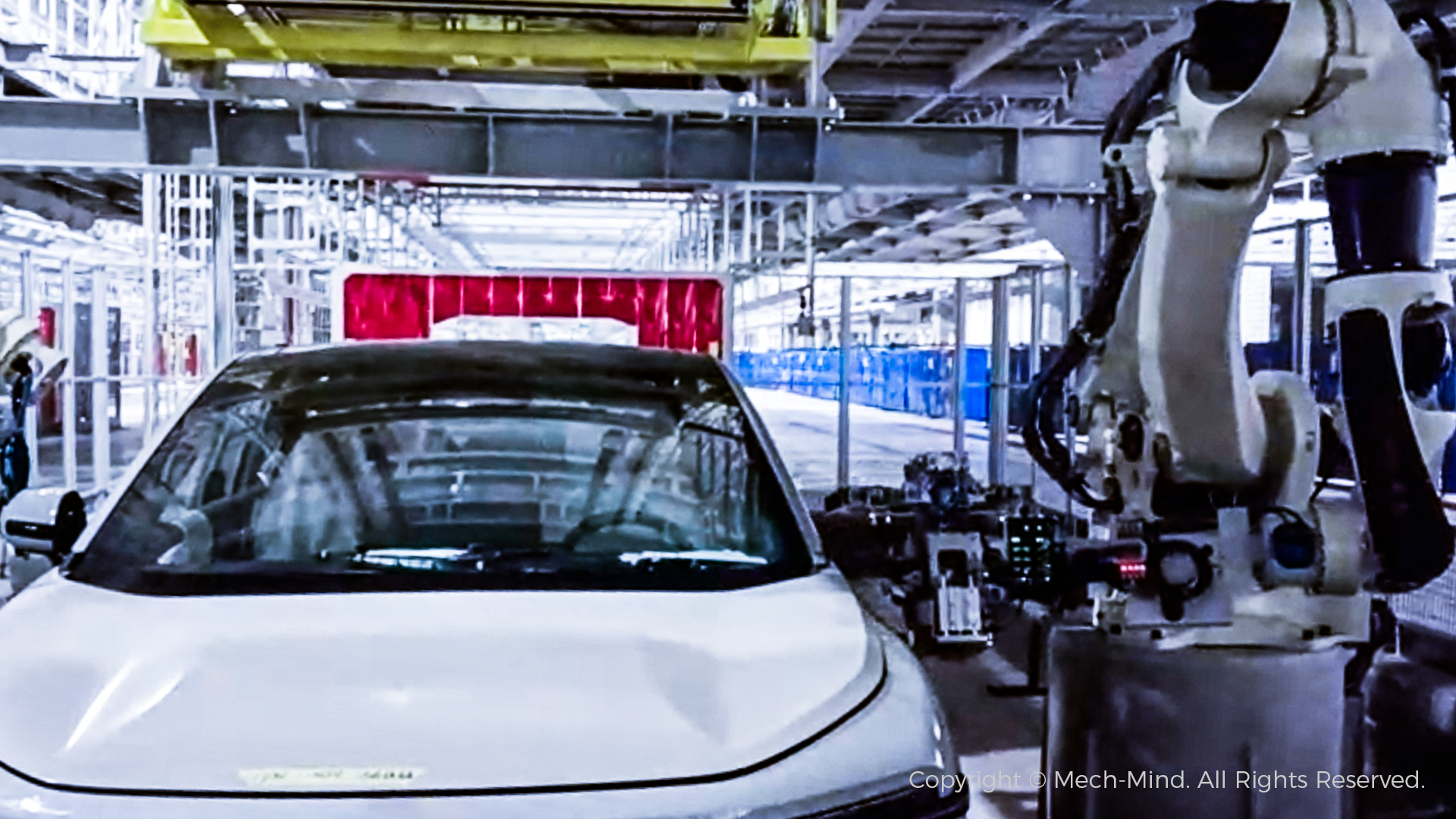
应用背景:
座椅安装质量将直接影响汽车的舒适性及安全性。传统的投放方式需人工搬运座椅,并将其对准车身安装孔位投放。人工搬运和投放效率低、劳动强度大且易导致座椅和车身发生磕碰。3D视觉对型面复杂的座椅进行准确定位,引导机器人抓取并搬运至预装位置。
3D视觉高精度定位车身B柱基准孔位置,引导机器人将座椅准确投放至指定位置。
AI技术灵活适应不同车型和工况,3D视觉能够对位置多变的座椅和车身高精度定位,提升产线柔性。
- 3D相机采用臂载式安装,先后扫描位于两条输送线上的座椅和车身,灵活度高。
4.内饰线:AI+机器人进行密封条辊压
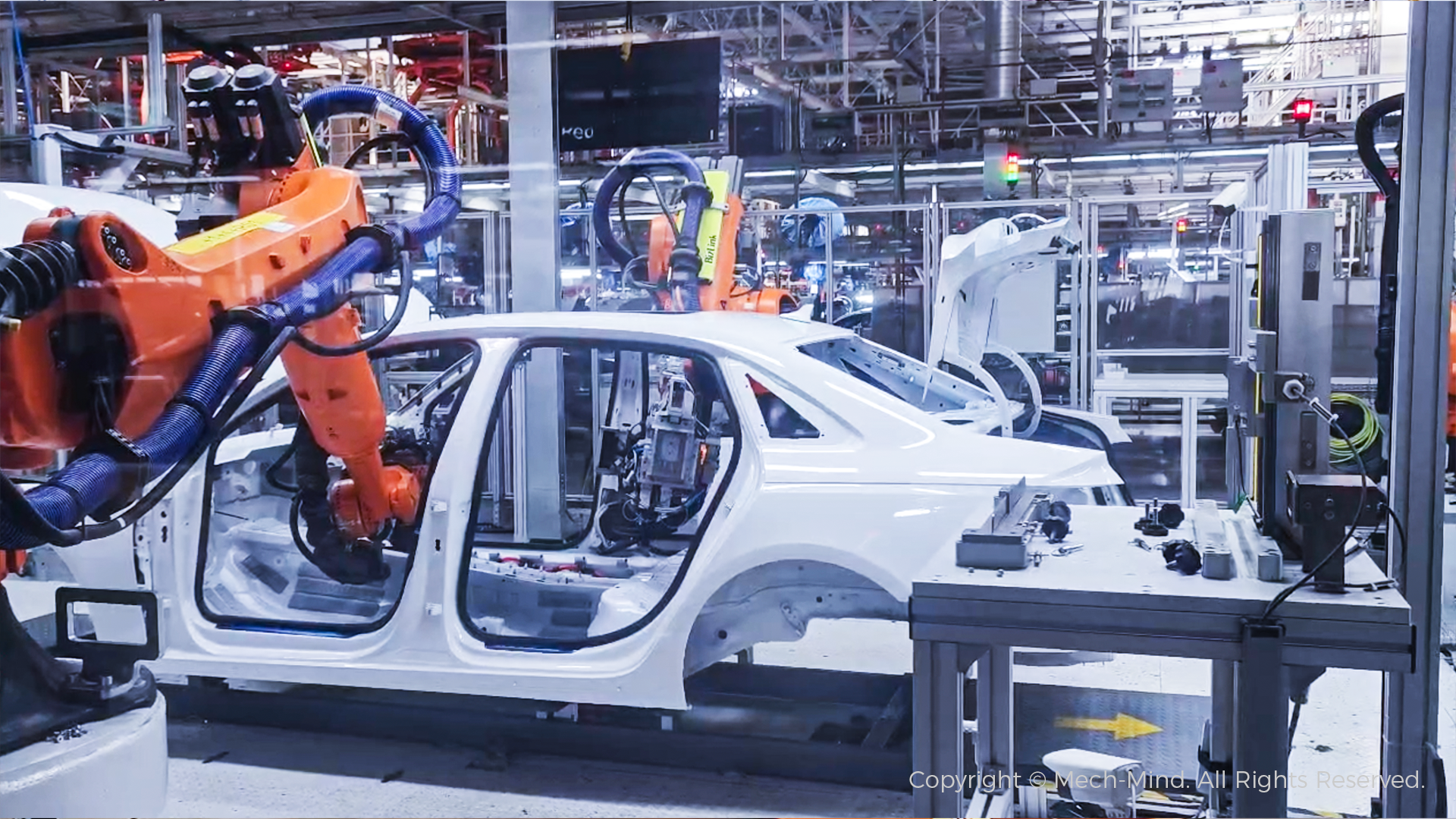
应用背景:
密封条安装质量关系着汽车的密封性和防水性能。人工操作容易导致密封条安装不牢固或出现褶皱,影响最终的密封效果。3D视觉系统能够高精度定位安装区域,确保密封条精准压入卡槽。
Mech-Eye工业级3D相机体积超小,安装灵活,随机器人运动到B柱内侧对其微小特征孔进行扫描。
支持多种不同车型,快速切换不同规格的密封条,无需频繁调整设备。
可适应车身到位偏移,有效计算偏移量并进行辊压轨迹纠偏,确保密封条安装牢固、平整。
5.底盘线:AI+机器人进行底盘拧紧
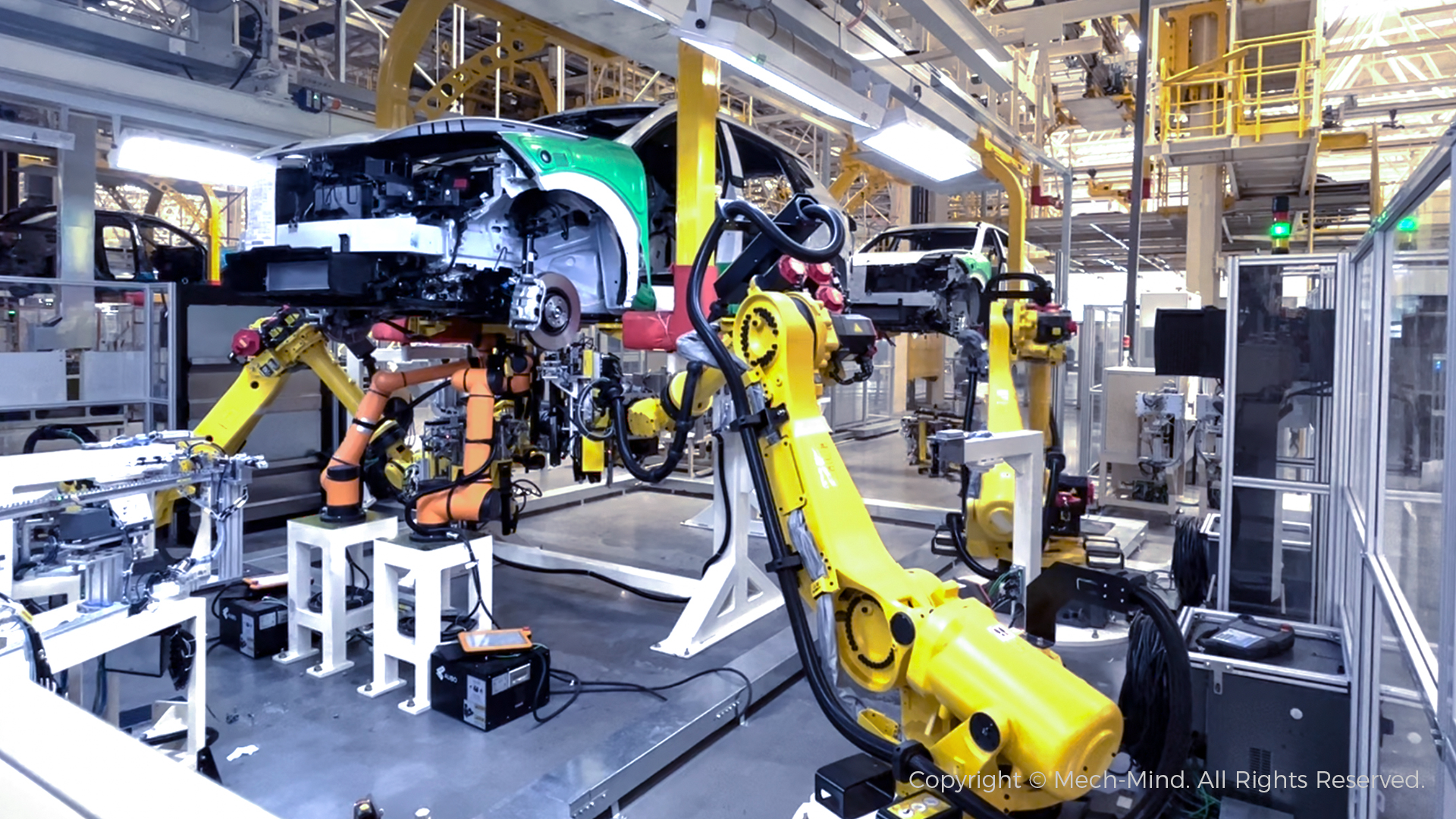
应用背景:
底盘拧紧是将底盘部件通过螺栓固定到车身上的过程,关系到车辆的操控性、安全性和耐久性。人工拧紧难以保证每次的力度和角度一致,且易出现螺栓漏拧的问题。
3D视觉能够对底盘螺栓高精度定位,实现精准拧紧。
可应对底盘部件位置多变、拧紧点分布复杂等问题,拧紧效率高。
消除人工误差,确保每次拧紧力度和角度一致,提升产品质量。
适应多车型对应的不同底盘结构,变更车型时的维护、调试成本大幅降低。
6.外饰线:AI+机器人进行风挡玻璃安装
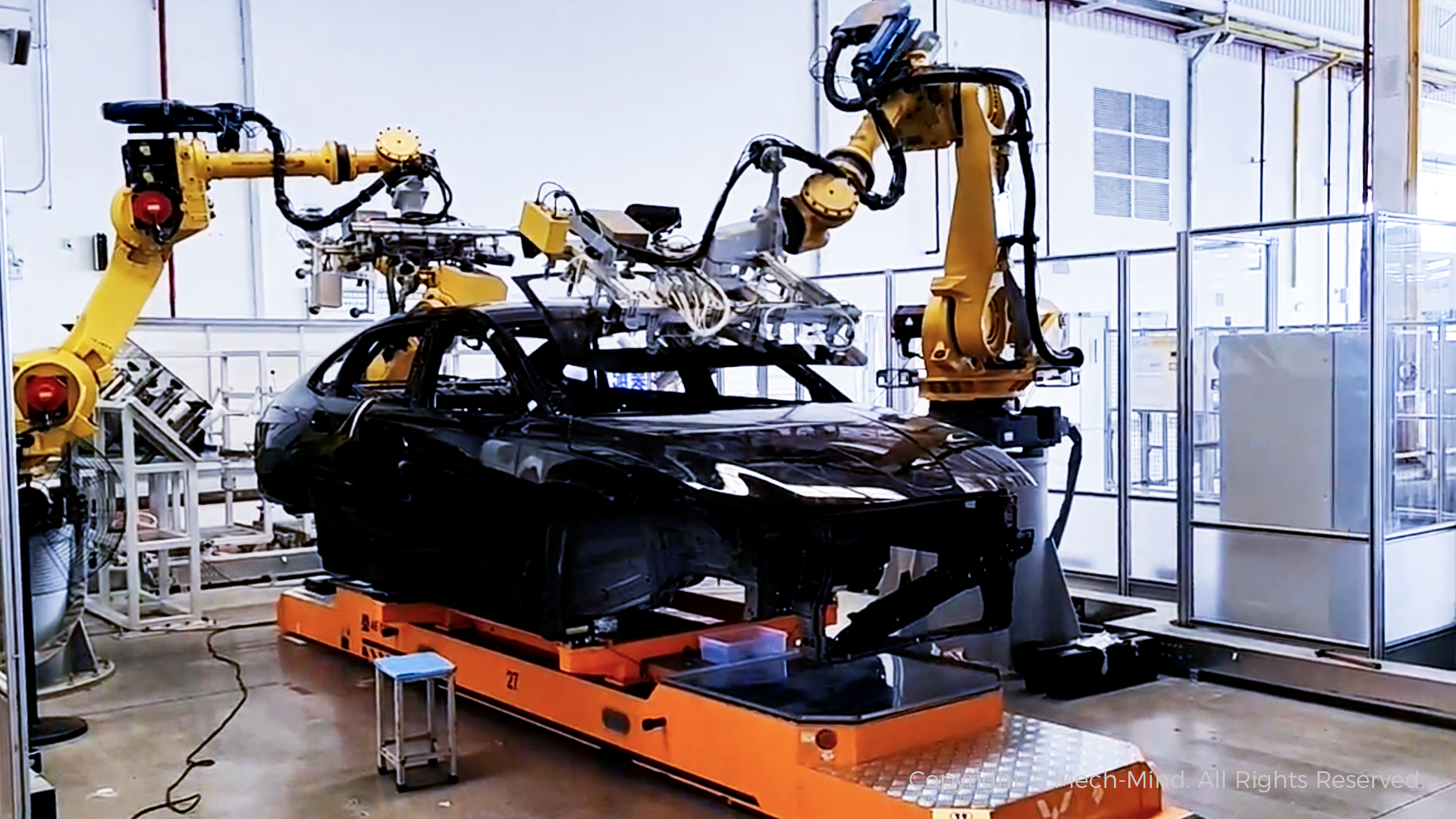
应用背景:
汽车风挡玻璃的安装质量会影响车辆的密封性及美观性。传统人工+机械辅助易出现偏差,导致玻璃安装不牢固或密封不良,且效率难以满足大规模生产的节拍要求。高精度定位车身安装区域,精准安装风挡玻璃,极大程度降低装配误差。
先进成像算法,在现场复杂光线的干扰下,可对漆面反光的车身高质量成像。
能够自动适应不同形状的玻璃和不同颜色的车身,支持多车型混线生产。
玻璃安装一致性好,效率满足高节拍生产需求。
7.外饰线:AI+机器人进行乘用车轮胎装配
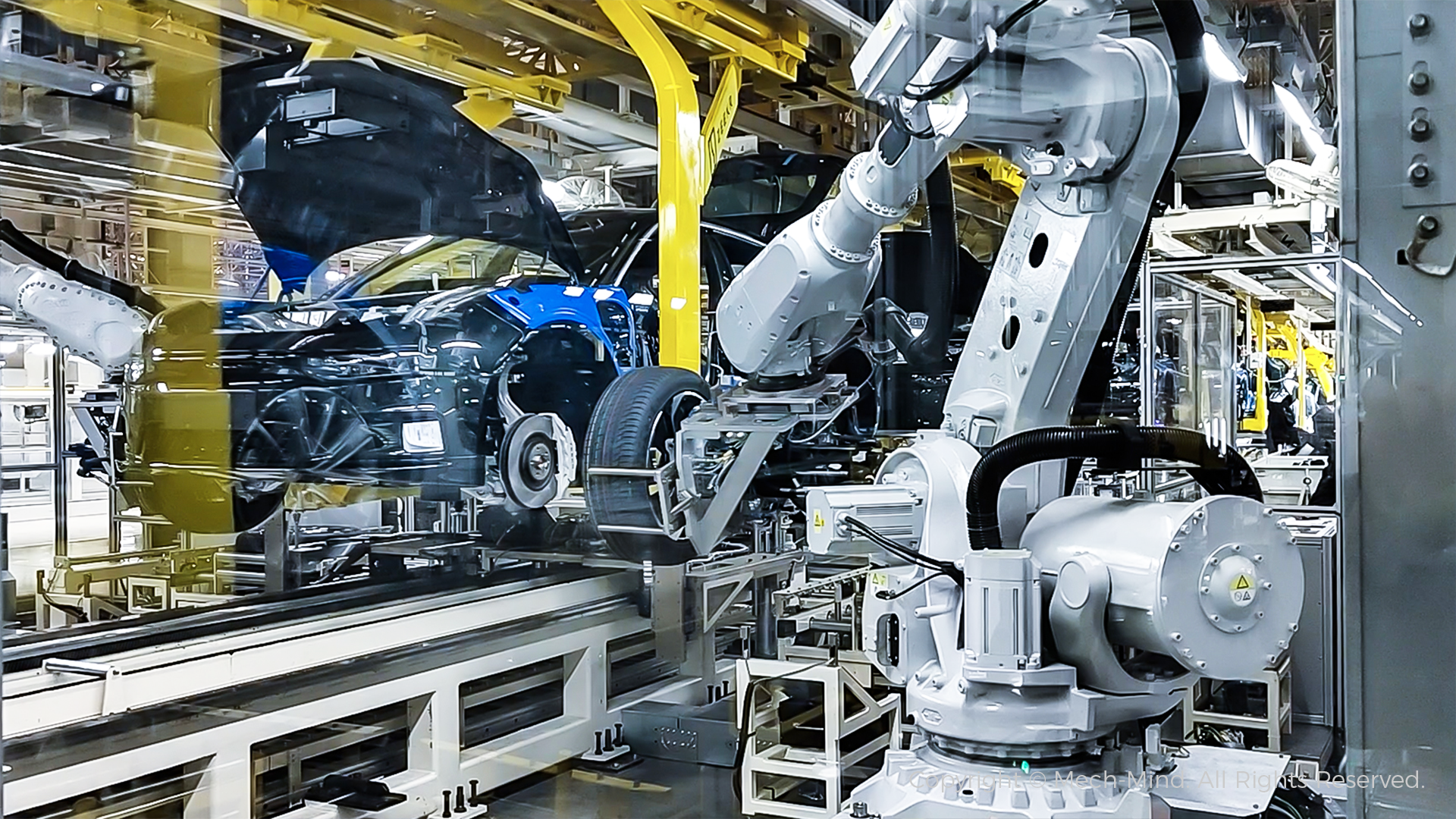
应用背景:
乘用车轮胎装配需要高精度和高效率,人工操作+机械辅助的方式效率受限。- 自研抗反光成像算法,可对表面高亮反光的刹车盘高质量成像;3D视觉高精度定位装配孔,引导机器人完成装配。
- 在切换产品规格时,AI算法可快速调整装配策略,减少换型时间。
- 路径规划+碰撞检测,保证抓取和装配的稳定性,更好适应随行装配。
- 已实现自动化生产,满足高节拍生产需求,提升客户产能。
8.外饰线:AI+机器人进行商用车轮胎装配
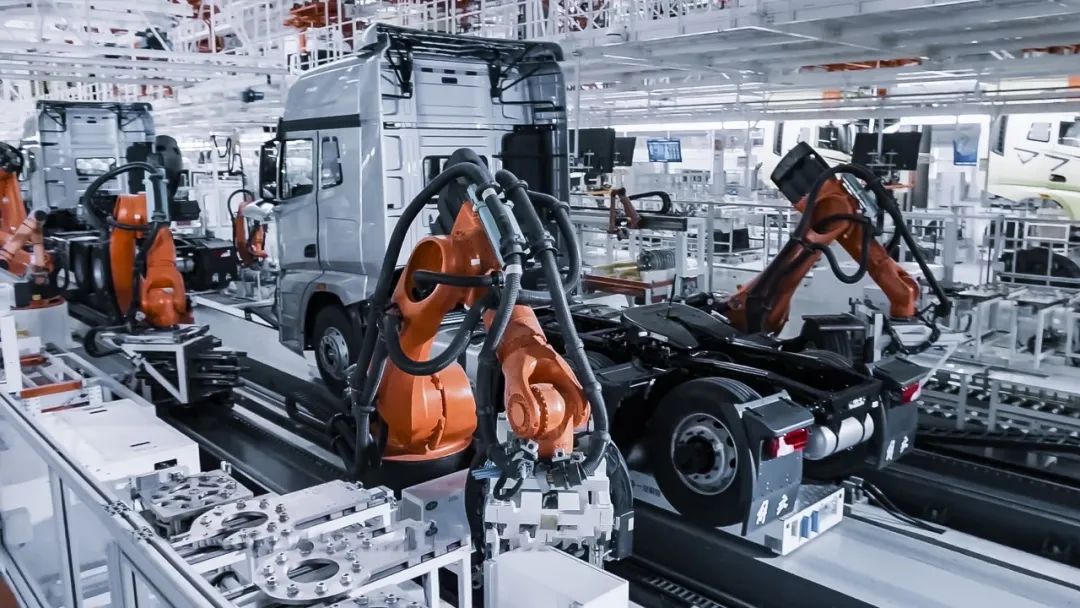
商用车轮胎重量可达上百斤,人工装配强度大、耗时长。车身置于主线滑橇上,装配过程需随滑橇动态进行,存在车身在滑橇上位置不固定、车轮转向角度存在偏差等问题。- AI+机器人完成了重卡前桥、中桥、后桥轮胎高精度随行装配,中桥、后桥为双轮胎装配。
- 3D视觉系统精确提取轮毂特征并定位,引导机器人将轮胎准确装入轮毂。
- 3D视觉能够实时捕捉到位有偏差轮毂的三维信息,确保装配过程的精度和效率。
9.外饰线:AI+机器人进行前端模块安装
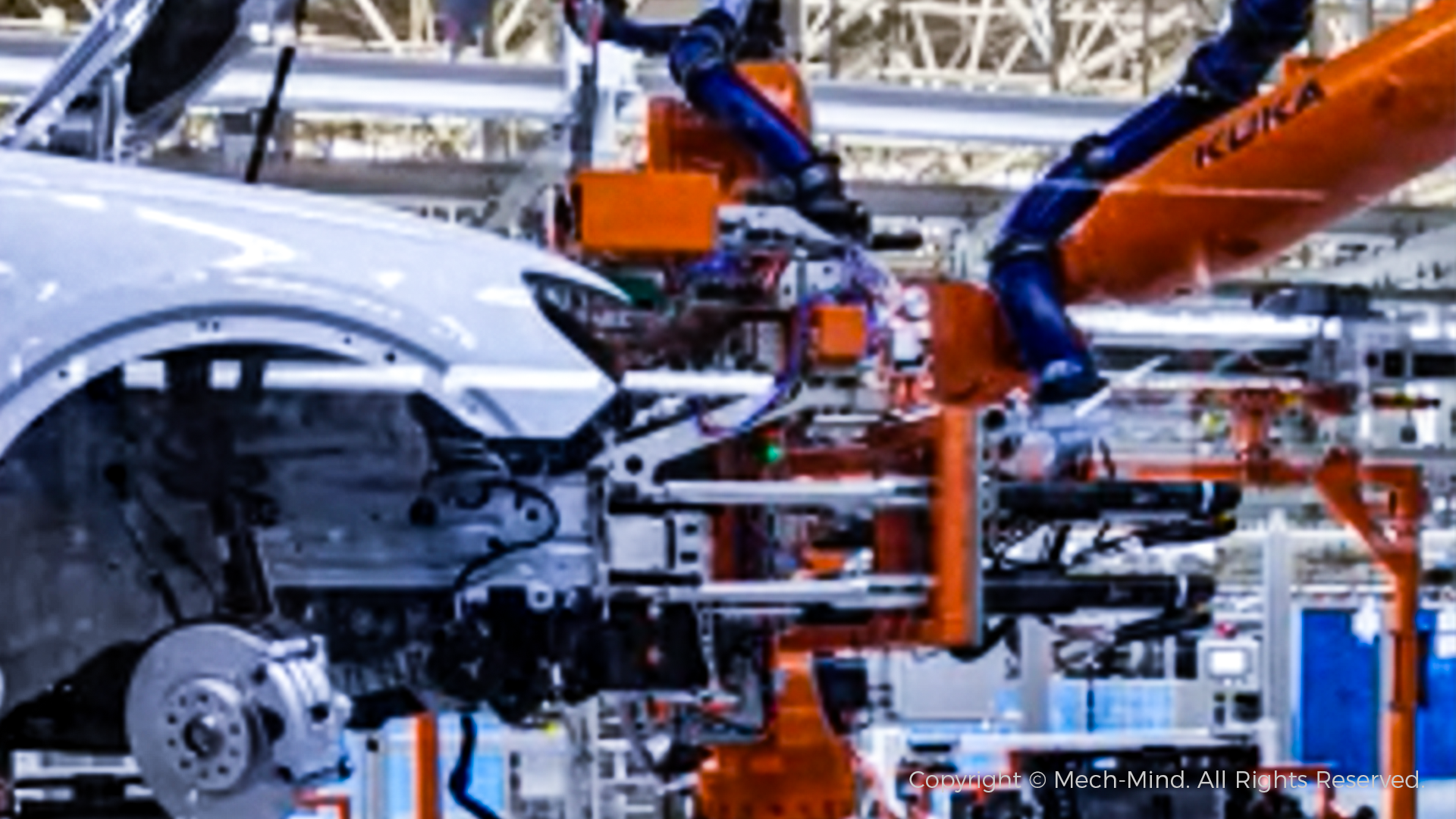
前端模块通常包括散热器、保险杠、大灯、发动机罩等部件,其安装过程对精度和效率要求非常高。传统工艺中,前端模块的安装主要依赖人工操作,存在效率低、精度不稳定等问题。- 3D视觉能够高精度识别定位前端模块和车身安装区域的姿态及位置,引导机器人精准抓取前端模块并进行合装拧紧。
10.质量检测:AI+机器人进行车身定位
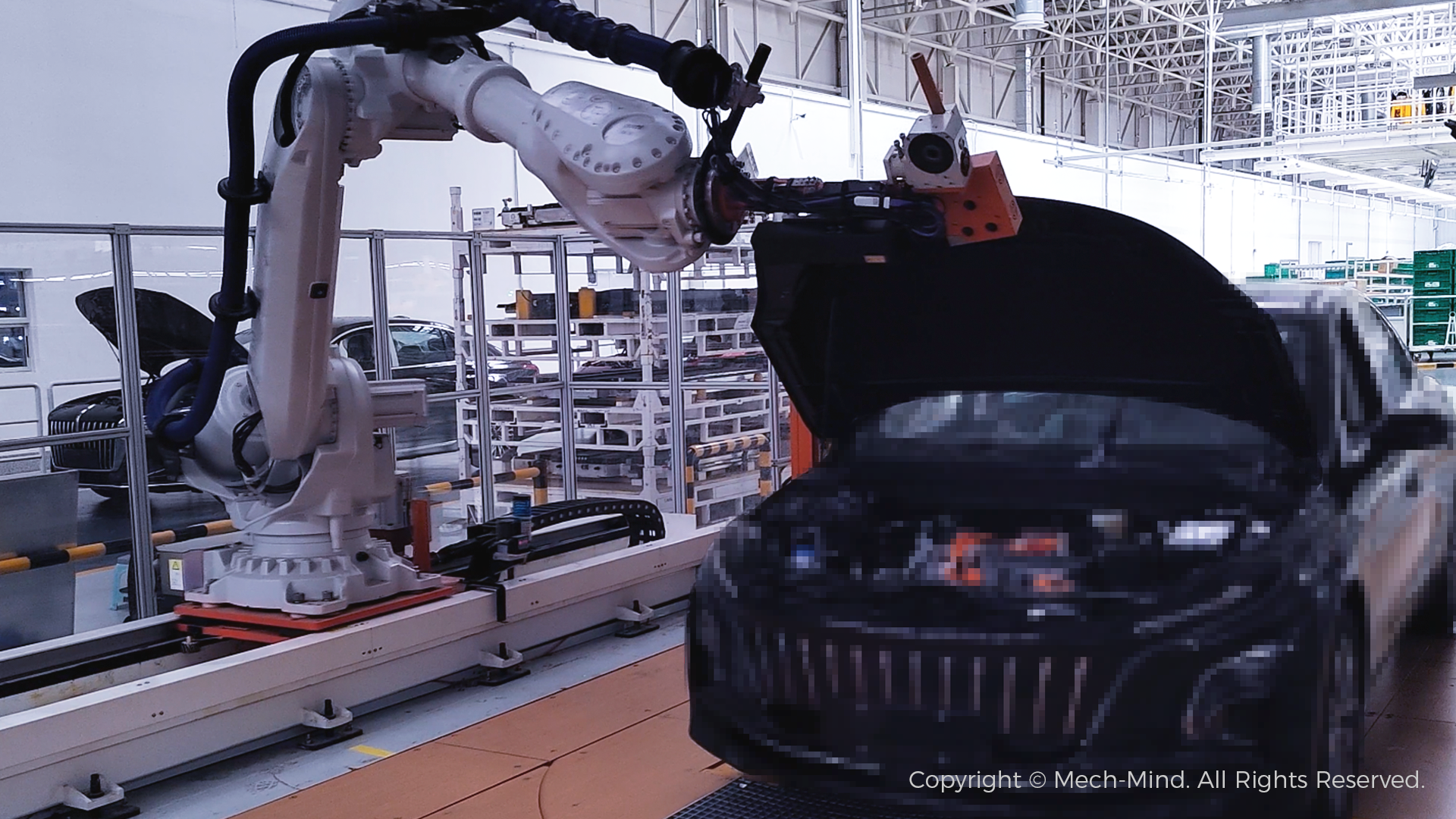
在进行间隙面差测量之前,车身必须经过精确定位,以确保测量结果的可靠性。
梅卡曼德AI+机器人技术已在汽车主机厂众多应用场景中通过实际生产验证,为汽车制造的自动化和柔性化提供了有力的技术支持。通过赋予机器人更精准的感知和执行能力,并结合对AI大模型的深入探索,梅卡曼德将持续赋能汽车工业的智能化升级与发展。