铅蓄电池具有高安全性、低成本、易充电、易回收等特性。但由于重量大、存在有害物质等原因,铅蓄电池生产制造环节催生了大量的自动化需求。
铅蓄电池是汽车行业主要使用电池类型。某头部储蓄电池企业在其汽车铅蓄电池注酸环节,引入了梅卡曼德3D视觉引导机器人进行铅蓄电池自动化拆垛。有效提升了铅蓄电池生产环节自动化水平,助力铅蓄电池安全、高效生产。
项目难点
铅蓄电池主要由正极板、负极板、酸液、隔板、电池壳体和安全阀等组成。当前工艺需将封装完成、整垛来料的铅蓄电池拆垛,放置于输送线上。后道工艺为将酸液注入电池壳体。
01 客户痛点
铅蓄电池自重大(15-30kg),人工拆垛强度大,难以满足订单需求。
铅蓄电池含有铅、硫酸等有害物质,长期作业存在健康风险。企业急需自动化改造。
后道工艺需将酸液注入电池壳体,风险系数高,需上游工艺效率稳定。
人工搬运可能发生磕碰,破坏电池密封性能,导致电池使用过程出现漏液,造成安全隐患。
02 视觉挑战
物料情况:
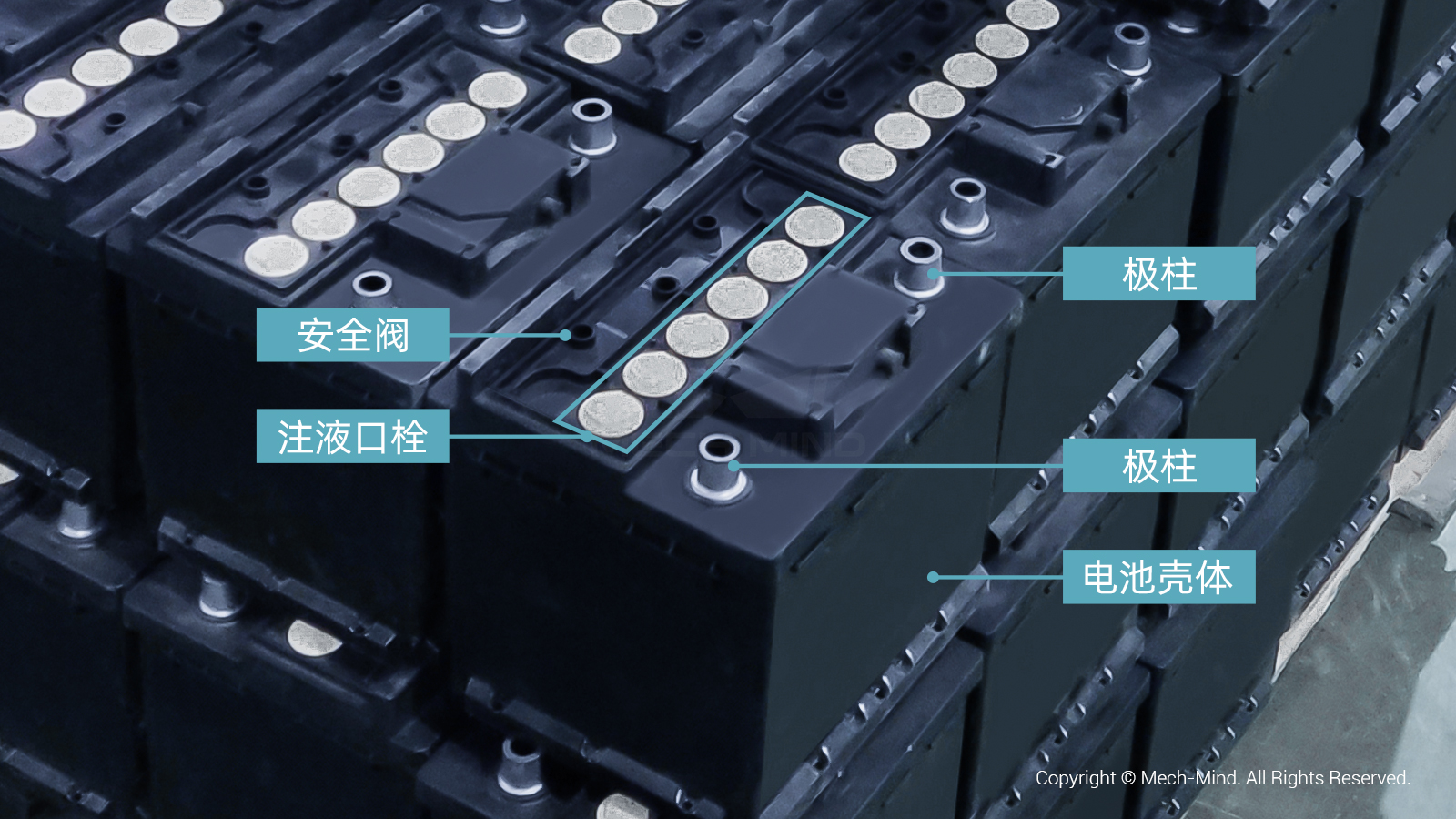
铅蓄电池基本结构
铅蓄电池壳体顶部为黑色,易吸光;型材结构复杂,有极柱、注液口栓、安全阀、各类凸起等。对于3D相机成像的对比度、清晰度要求高。
每层物料之间有隔板。单层物料和整垛拆垛完成后,3D视觉系统需自动识别定位隔板及托盘,引导机器人抓取。
现场有数十种铅蓄电池,每垛一种产品,不同垛位产品码放方式不同。3D视觉系统需兼容不同产品及垛型。
现场工况:
铅蓄电池紧密贴合码放在托盘上,由输送线运输到位,可能存在托盘到位偏移、电池错位等情况。3D相机需具备大视野、大景深的特点,并在远距离安装的情况下完整覆盖垛位,保持高精度成像。
下游工艺注酸设备位置固定,每次来料的铅蓄电池要保证朝向一致。需3D视觉系统精准定位电池位姿,判断铅蓄电池朝向。
3D视觉系统需准确判断当前产品种类、尺寸,进行多抓规划。
现场布局紧凑,设备、支架较多。并要留有足够的空间供机器人在托盘、输送线之间自由移动。3D视觉系统需具备路径规划与碰撞检测能力。
解决方案
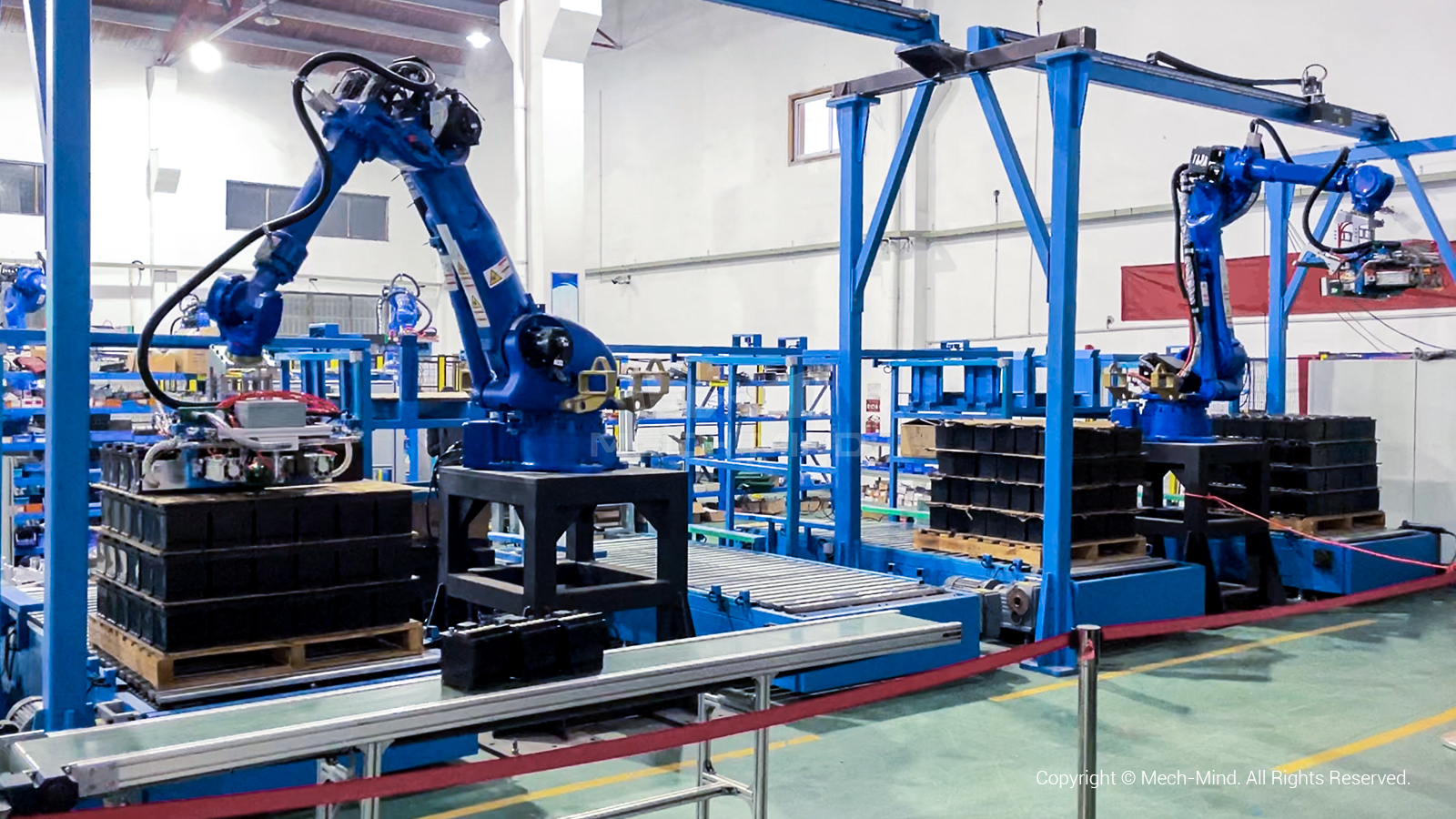
项目现场
3D相机选型及安装方式:Mech-Eye DEEP,固定安装于滑轨上。
3D相机拍照距离:2000 mm(相机底部到产品上表面的距离)。
满垛尺寸:1250×1250×1000 mm
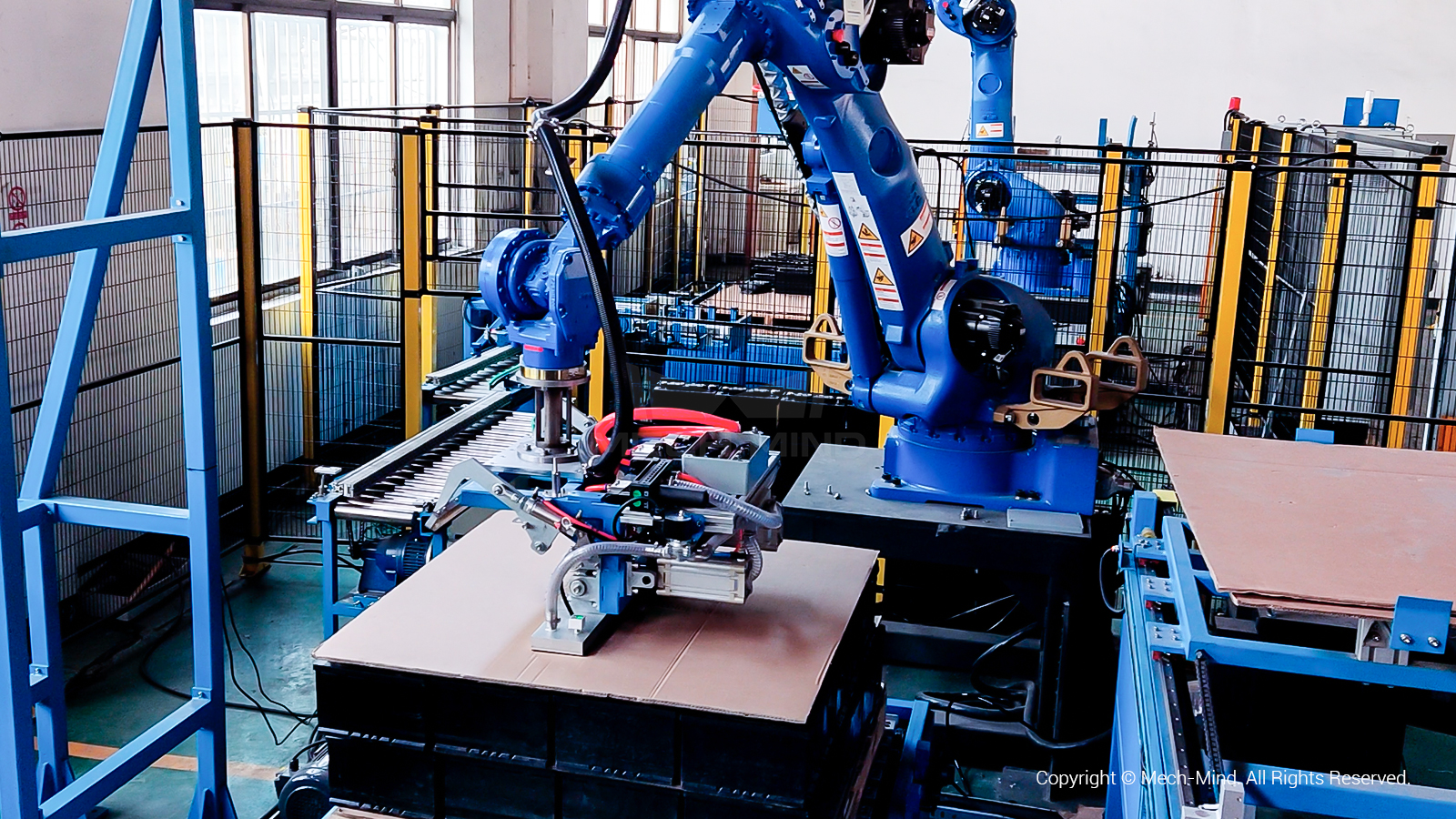
方案优势及收益
01 方案优势
性能强大、灵活易用的工业级3D相机
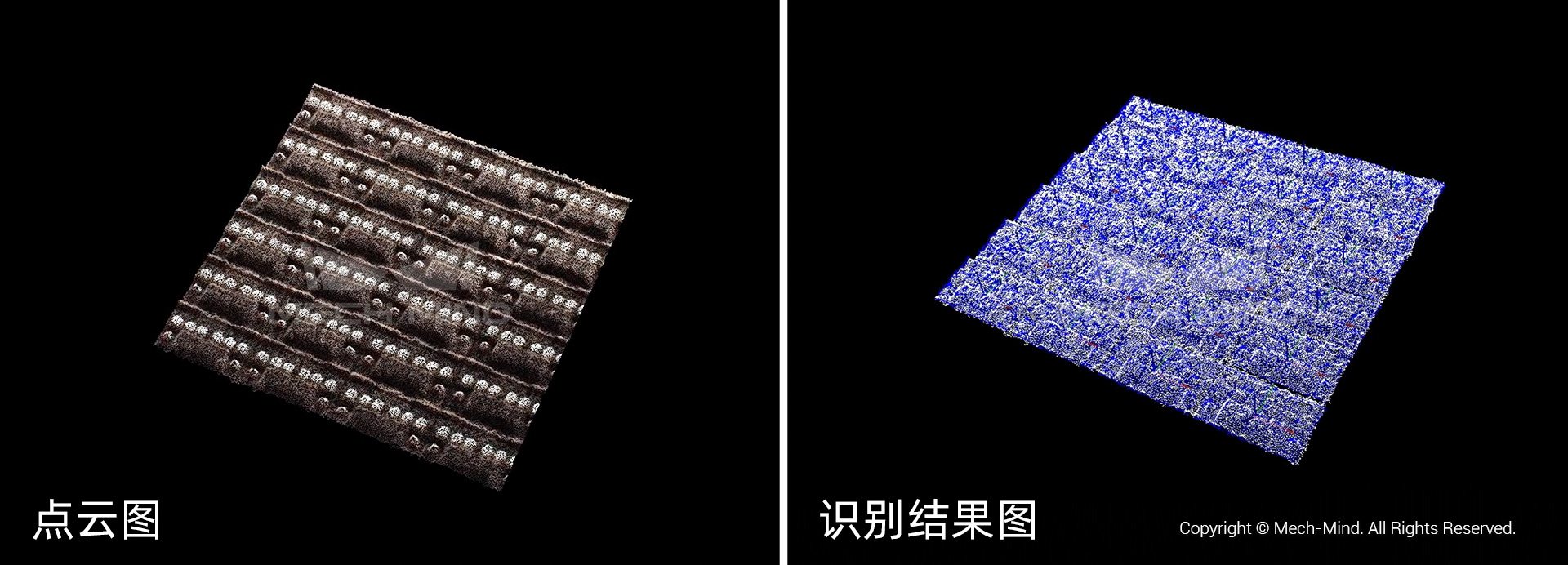
紧密贴合的铅蓄电池
Mech-Eye DEEP @ 2.0 m
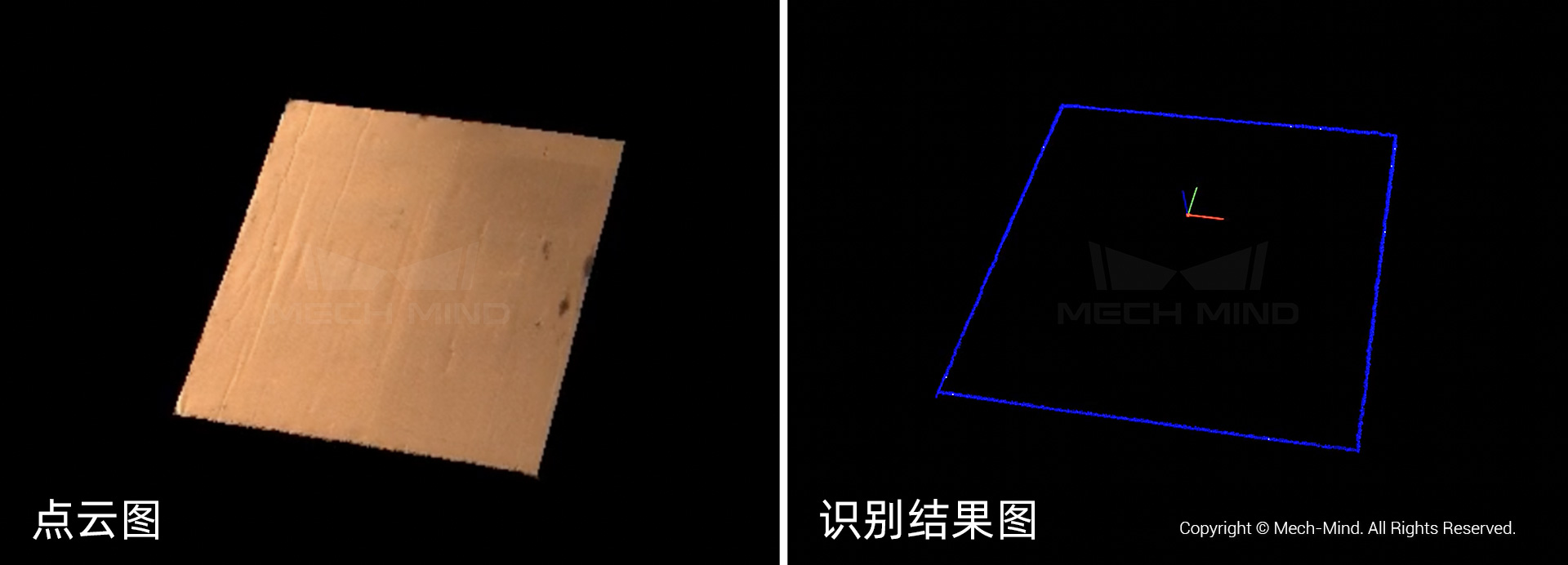
隔板,Mech-Eye DEEP @ 2.0 m
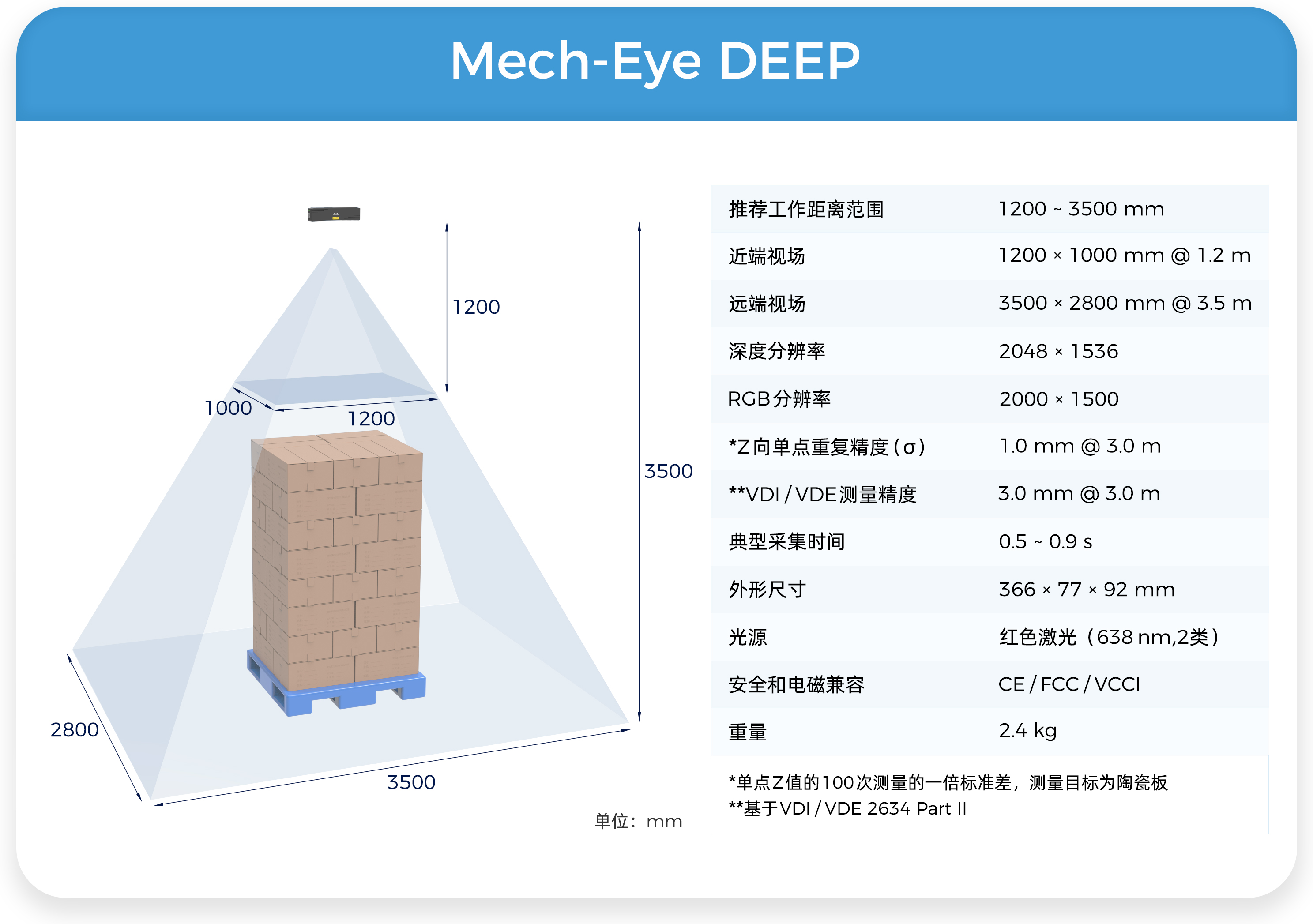
Mech-Eye DEEP 核心参数
智能规划抓取
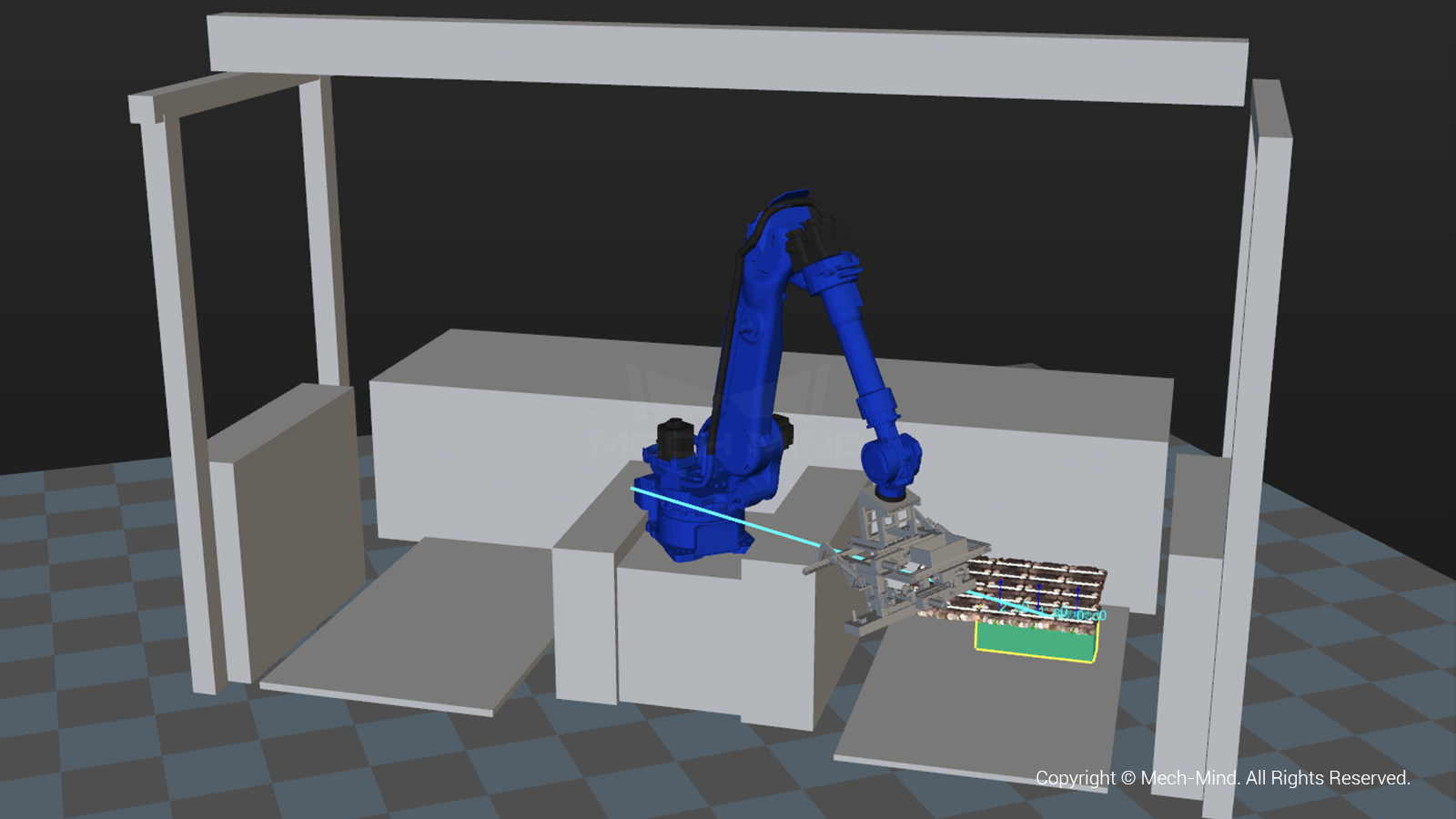
智能规划抓取
3D视觉系统与机器人、夹具高度集成,根据获取的铅蓄电池种类、尺寸信息,进行多抓规划。
结合物料种类、形态设置相应抓取策略:隔板/托盘(吸取)、紧密贴合的铅蓄电池(抱夹+拖拽式抓取)。
3D视觉系统稳定区分电池朝向。智能规划抓取顺序及数量,实现单次抓取数量最多的同朝向铅蓄电池,提升生产效率。
先进AI算法,精准稳定抓取
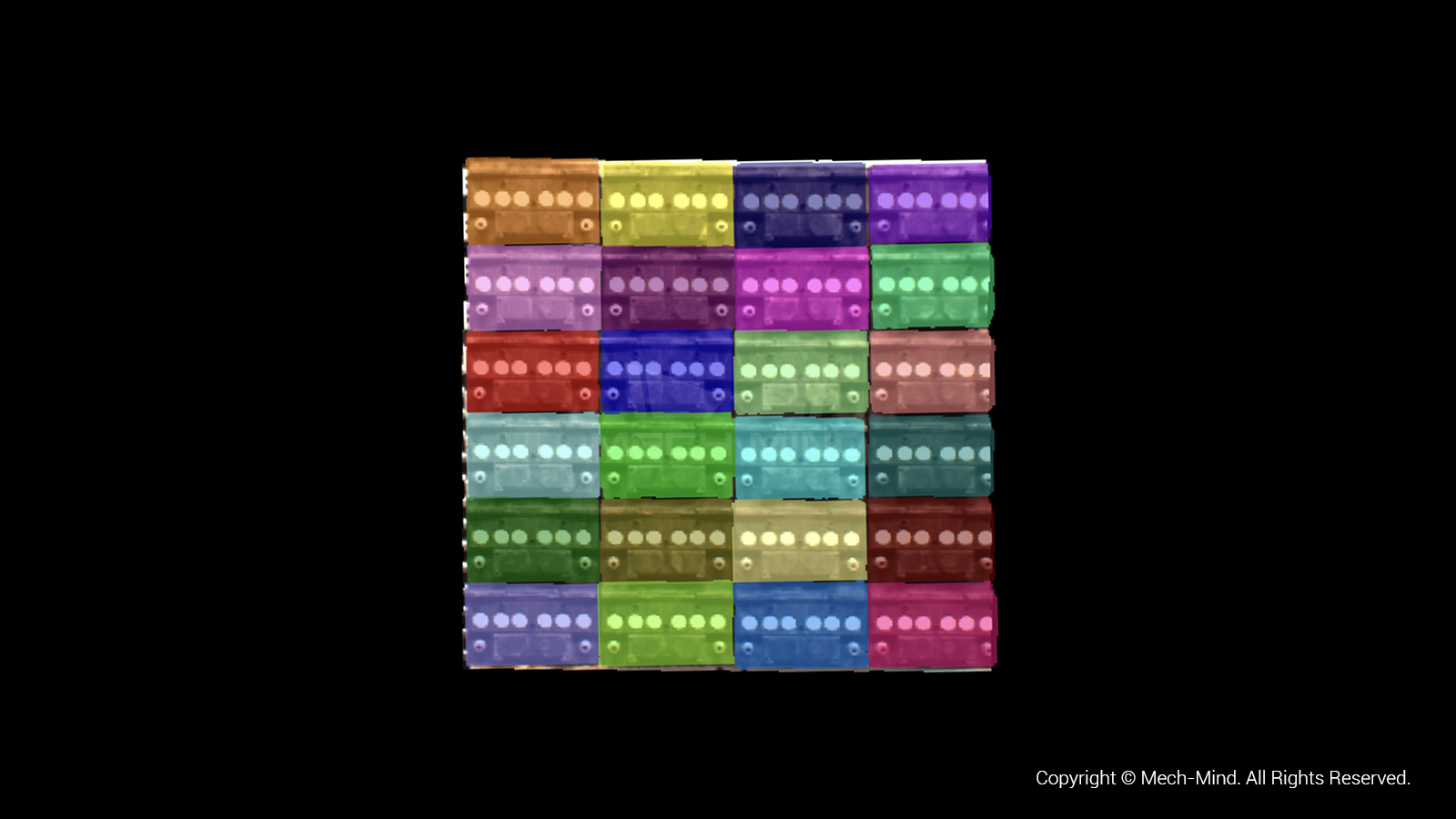
智能规划抓取
深度学习算法+高精度模板匹配,精准分割紧密贴合的铅蓄电池,引导机器人精准抓取,保证铅蓄电池密封性能。
运动仿真+碰撞检测,规避多抓过程中可能发生的干涉。快速生成无碰撞的轨迹,引导机器人稳定抓取。
支持现场数十种不同种类的铅蓄电池,支持新增车型对应铅蓄电池的快速配置,迅速反应汽车市场变革需求。
02 项目收益
梅卡曼德深耕AI+3D视觉领域,致力于以标准化产品赋予工业场景更多可能。并配备了强大的交付及售后团队,为项目的顺利落地及后期维护提供强有力的支持,现已完成拆码垛、上下料、装配、涂胶等典型应用规模化落地。