惯性环是汽车发动机减震器中不可或缺的重要部件。在汽配厂惯性环生产车间,工件需经过铸造-粗加工-精加工-规格复检等数道工序,方能成为成品出库。加工过程催生了大量上料需求。
本案例中,梅卡曼德携手合作伙伴赋能某大型汽配厂,用AI+3D技术实现惯性环精加工环节上料自动化。智能机器人工作站配合CNC(数控机床)进行机加工,帮助终端客户显著提升生产效率、降低成本。
01 客户痛点
将惯性环置于CNC进行双面磨削并测厚,是其生产重要环节。自动化改造前,本案例客户使用人工进行上料,存在以下痛点:
· 惯性环尺寸大(外径300-500 mm不等)、质量大(8-40 kg),人工上料存在安全隐患,生产效率不稳定。
· 生产标准严苛。人工搬运不当易导致碰撞、剐蹭等问题,影响成品质量。
· 工件品规繁多,加工流程长,定位工装等额外成本高。
02 现场挑战
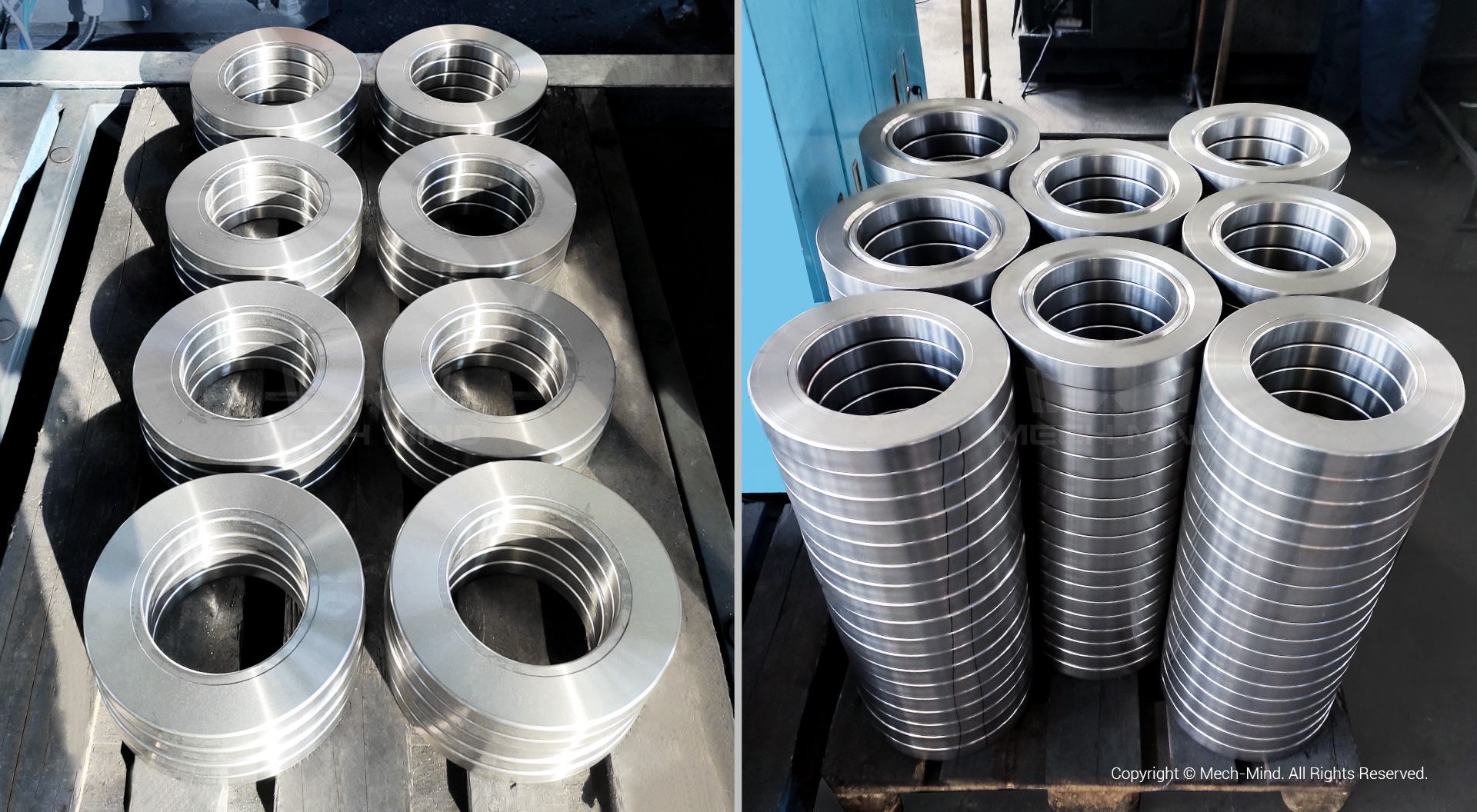
高亮反光的惯性环,上料工位伴随强烈阳光干扰
· 工件呈环状,表面覆油膜且反光,现场环境光干扰严重,对3D相机成像能力提出挑战。
· 工件尺寸大(外径300-500 mm不等)、堆叠层数多(10-15层不等,整垛高度约600-800 mm)、托盘面积较大(1200*800 mm),且上料精度要求高,3D相机需在远距离处高精度成像,景深也需满足需求。
· 现场布局紧凑,工序流程多,3D视觉系统需引导机器人配合CNC对惯性环进行双面磨削上下料。
· 工件及现场设备价值高、品控要求严格,机器人需稳定上下料,避免因碰撞、剐蹭造成损失。
· 工件品规多、更新频繁,生产节奏快。新增品规不能影响生产效率。
解决方案及优势
01 整体工作流程
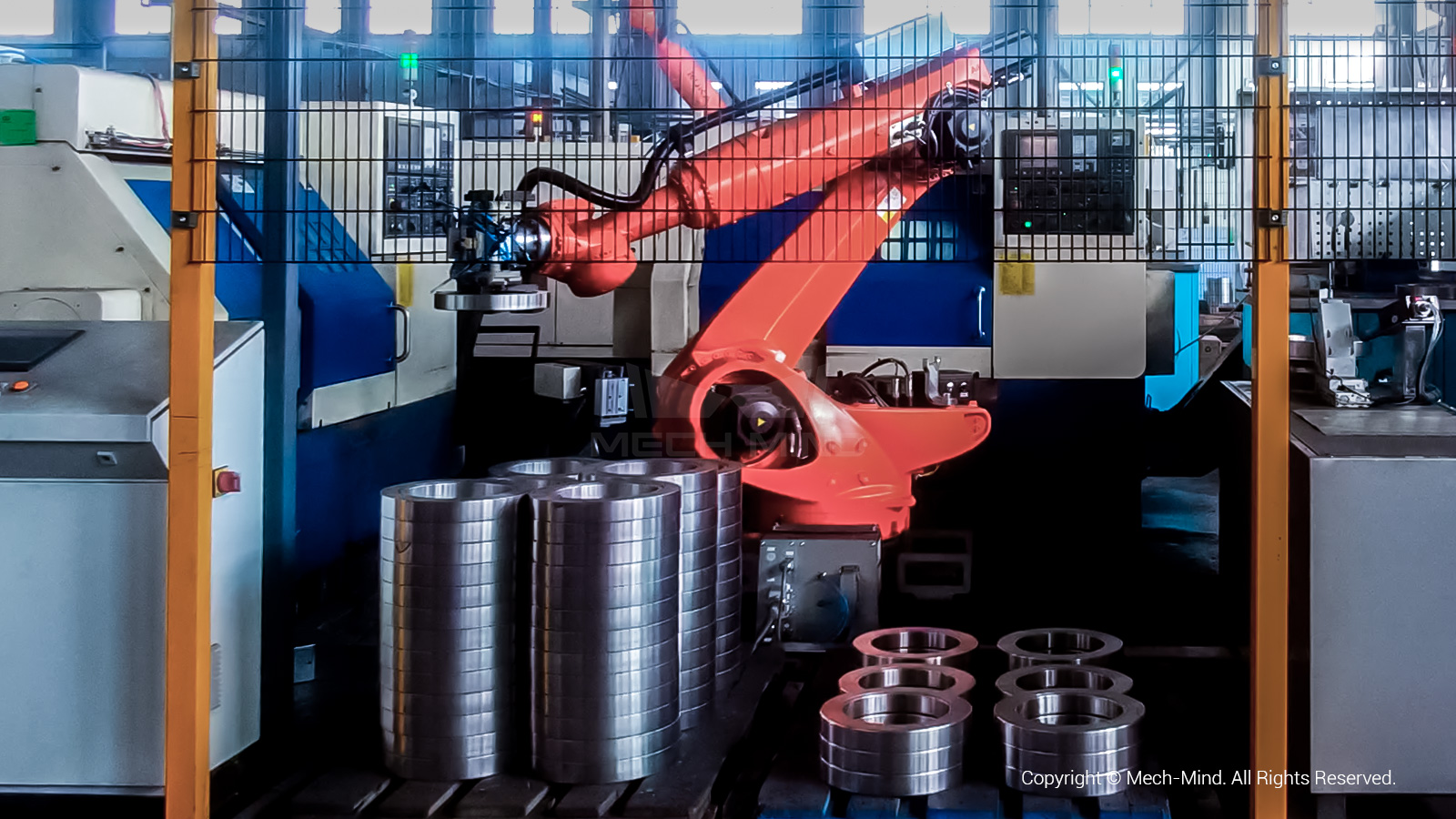
项目现场图
· 叉车运送整垛惯性环至上料位。
· 固定式安装的Mech-Eye LSR L工业级激光3D相机对整垛工件拍照,获取3D点云数据;Mech-Vision对点云进行处理,生成抓取点传输给机器人,机器人抓取单个工件放置于CNC加工。
· 单面加工完成后,机器人抓取惯性环下料并翻面,置于另一CNC对工件反面进行加工。
· 双面均加工完成后,机器人抓取惯性环至测厚工位进行厚度测量。
· 机器人将惯性环码放于另一托盘。
02 项目优势
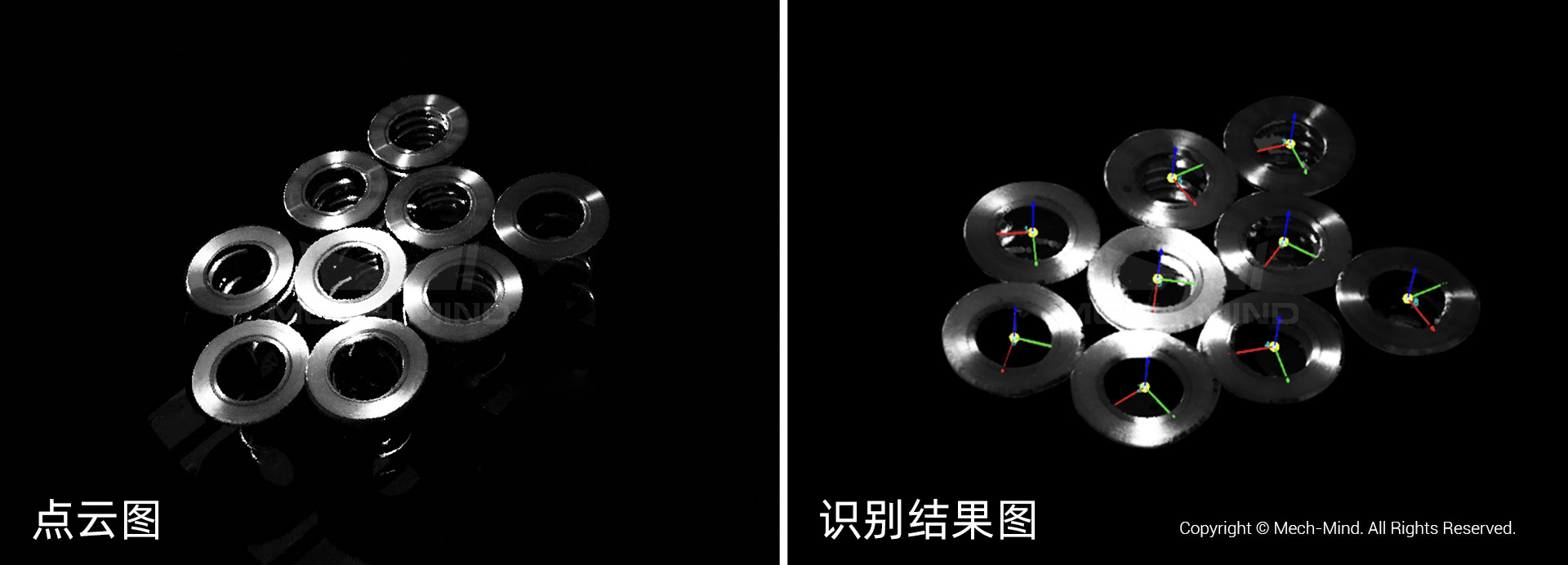
Mech-Eye LSR L @ 1.5 m
· 采用先进成像算法,Mech-Eye LSR L可适应不同时段、不同工位的光照变化。晴天阳光直射厂房条件下(> 20000 lx),也可对高亮反光工件高质量成像。
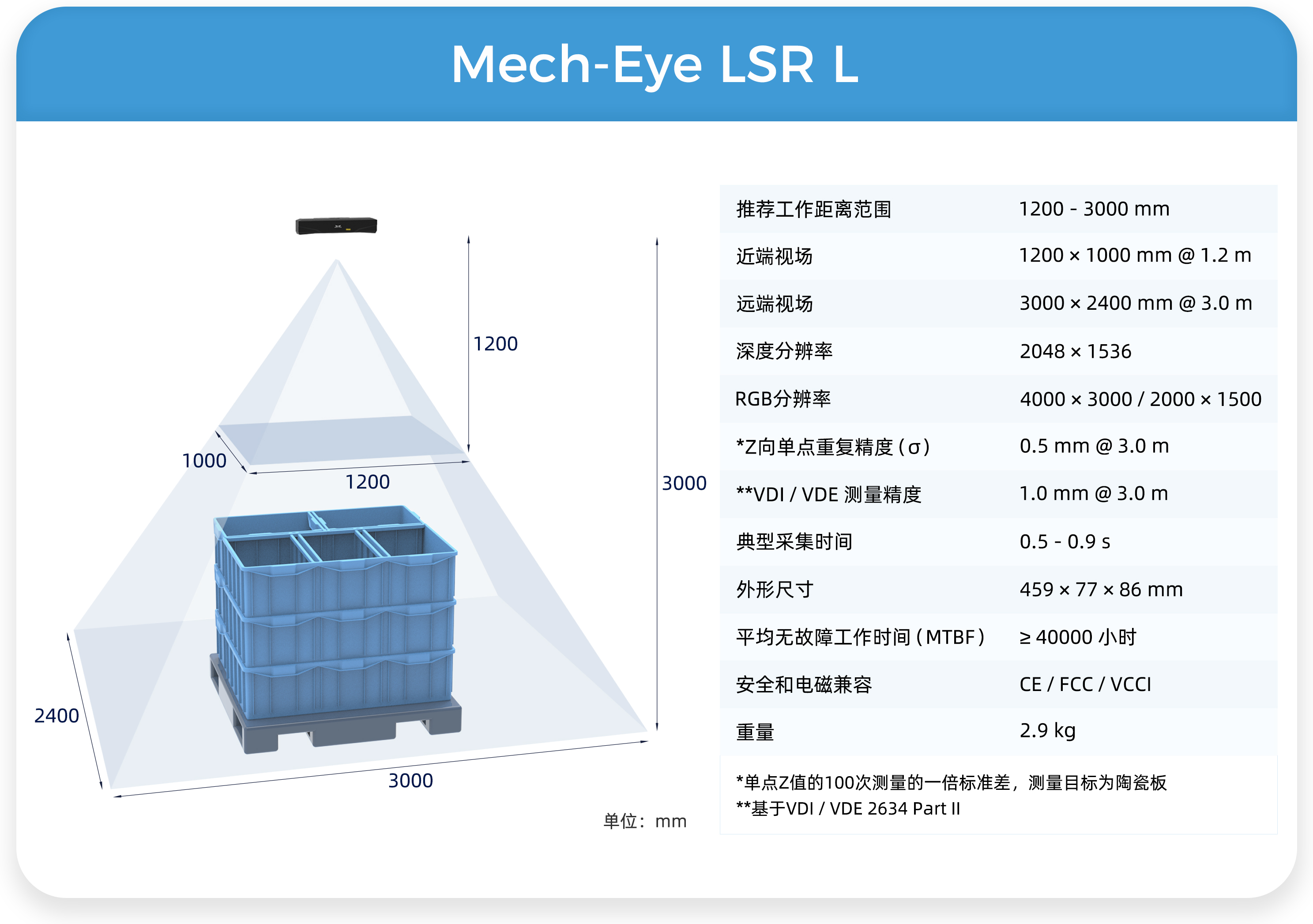
Mech-Eye LSR L主要参数
· Mech-Eye LSR L是梅卡曼德远距离3D相机旗舰机型,推荐工作距离1200-3000 mm。大视野、大景深,支持高精度大面积作业。适合于大工件、大托盘、深框抓取等场景。
先进视觉算法,支持十数种工件品规。快速实现多品规的柔性兼容。
· 新升级3D相机及视觉系统软件,性能及易用性全面提升。合作伙伴可快速将3D视觉系统与机械臂、夹具、CNC等设备无缝集成,满足终端客户多工序流转及生产要求。
03 项目成果
· 梅卡曼德3D视觉系统搭配合作伙伴整体方案,机器人可对惯性环稳定抓取,显著减少货损,提升生产效率。
· 该汽配厂启用智能机器人工作站后,产能提升3倍。
梅卡曼德已在全球知名汽配厂/主机厂落地1000+实际案例,应用范围涵盖上下料、装配、定位等。如您想了解更多信息,或想咨询汽车行业解决方案,请发送邮件至info@mech-mind.net。