焊装又称“机械裁缝”,是指将冲压成型的工件焊装成底板、顶盖、侧围等分总成,再合装成白车身总成的过程。在焊装线体上,存在大量EMS/料车/料箱抓放件需求。为了组焊成高精度总成,以往主机厂会采用机器人示教+高精度工件限位完成抓放件。但综合成本、产能、设备生命周期等方面考虑,此种方式无法实现生产效益最大化。
梅卡曼德将AI+3D视觉技术与汽车制造工艺相融合,面向焊装场景推出了3D视觉引导抓放件系统。工位通过引入该系统,对工件的型号、位姿进行判断和纠偏,引导机械臂完成精准抓放。“AI+机器人”智能工作站不仅满足了汽车柔性制造的需求,也从工艺执行质量、产能目标、成本控制等方面为主机厂客户保驾护航。
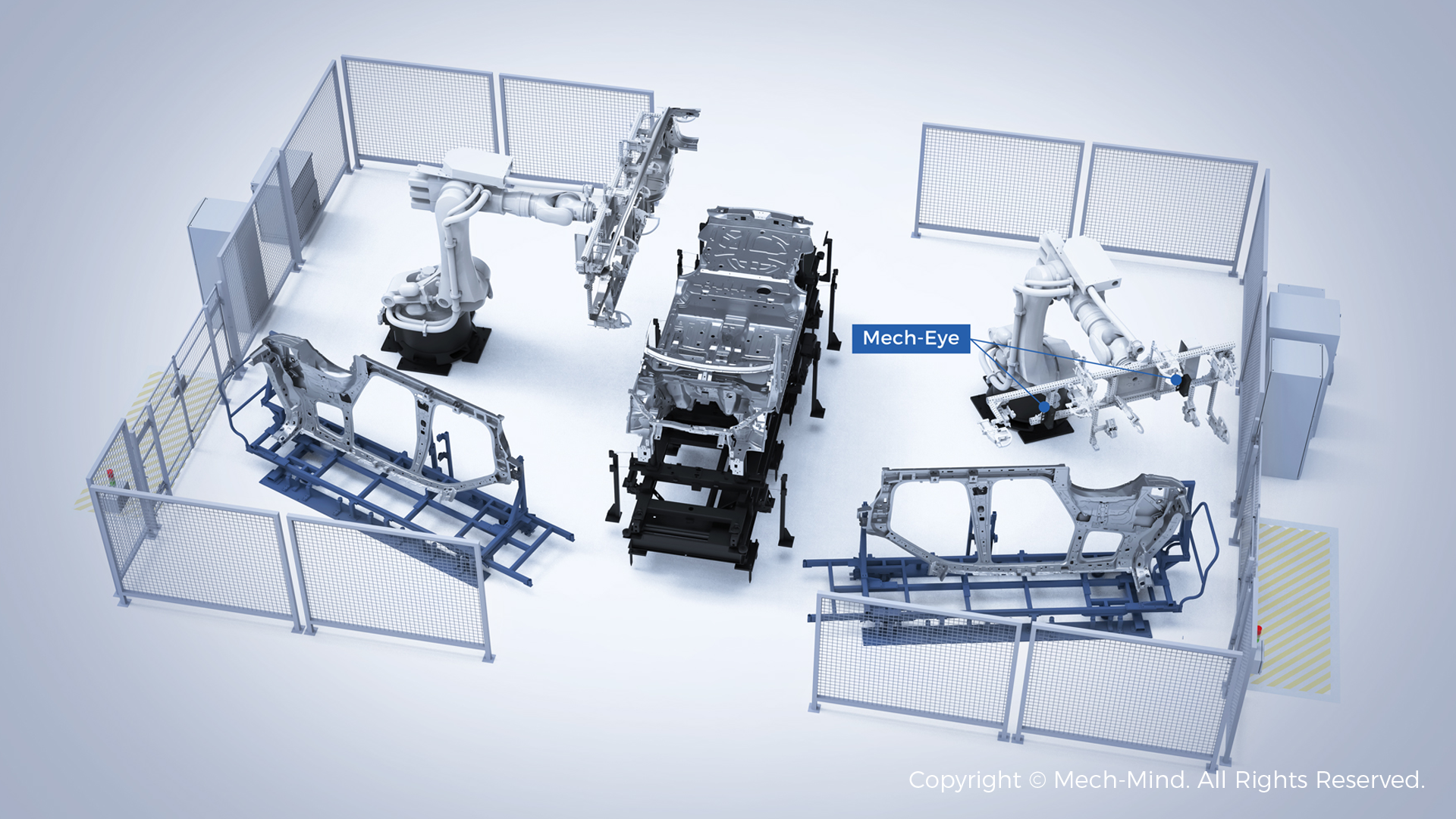
梅卡曼德3D视觉应用于焊装车间抓放件
01 高性能3D视觉引导系统
精准抓放,助力焊装自动化
传统焊装线,机器人示教抓取需将被抓工件置于高精度定位工装上,存在示教流程繁琐、精盛具造价高昂等问题。
梅卡曼德3D视觉引导抓放件系统,很好地解决了待抓取物料需高精度限位问题。该系统主要由梅卡曼德高精度结构光3D相机Mech-Eye PRO S-THR/M-THR、Mech-Vision机器视觉软件组成。基于先进的光学器件和成像算法,3D相机可对深色吸光、高亮反光、粉尘/锌层覆盖的车身件生成高质量3D点云数据。Z轴精度高,轻松应对来料位置偏差很大的工况。产品结构紧凑,安装于机械臂上完成对工件特征三维信息的提取,灵活度高。
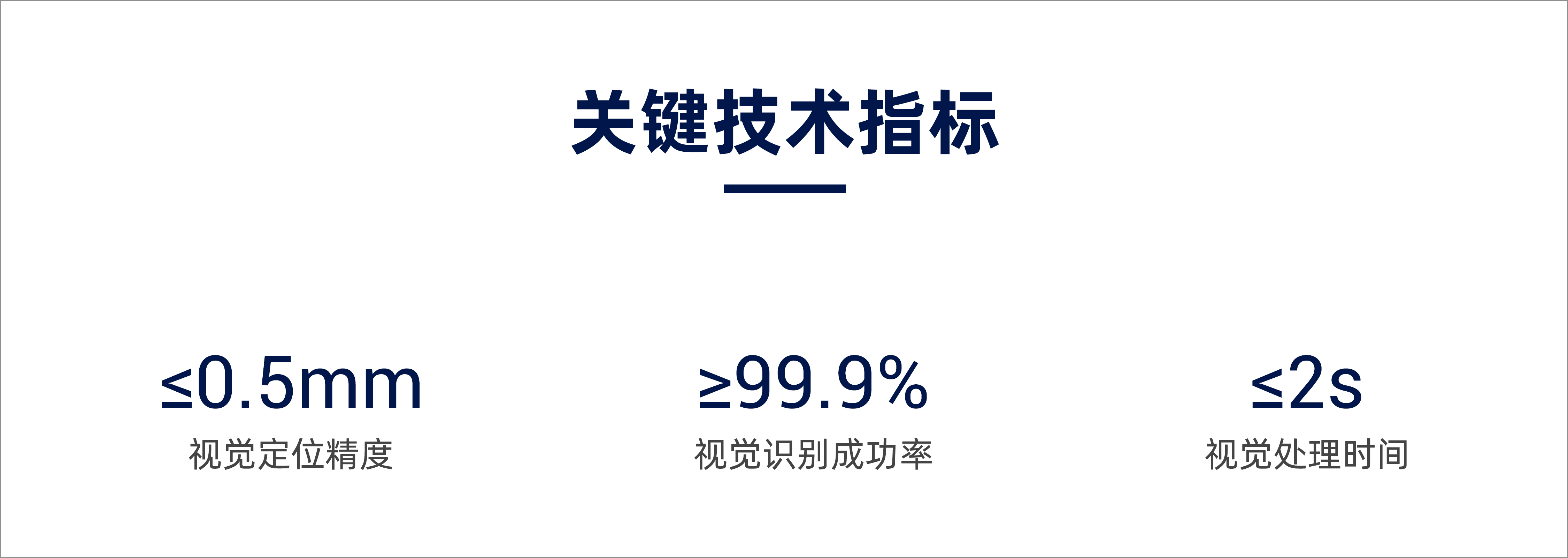
核心技术指标业界领先
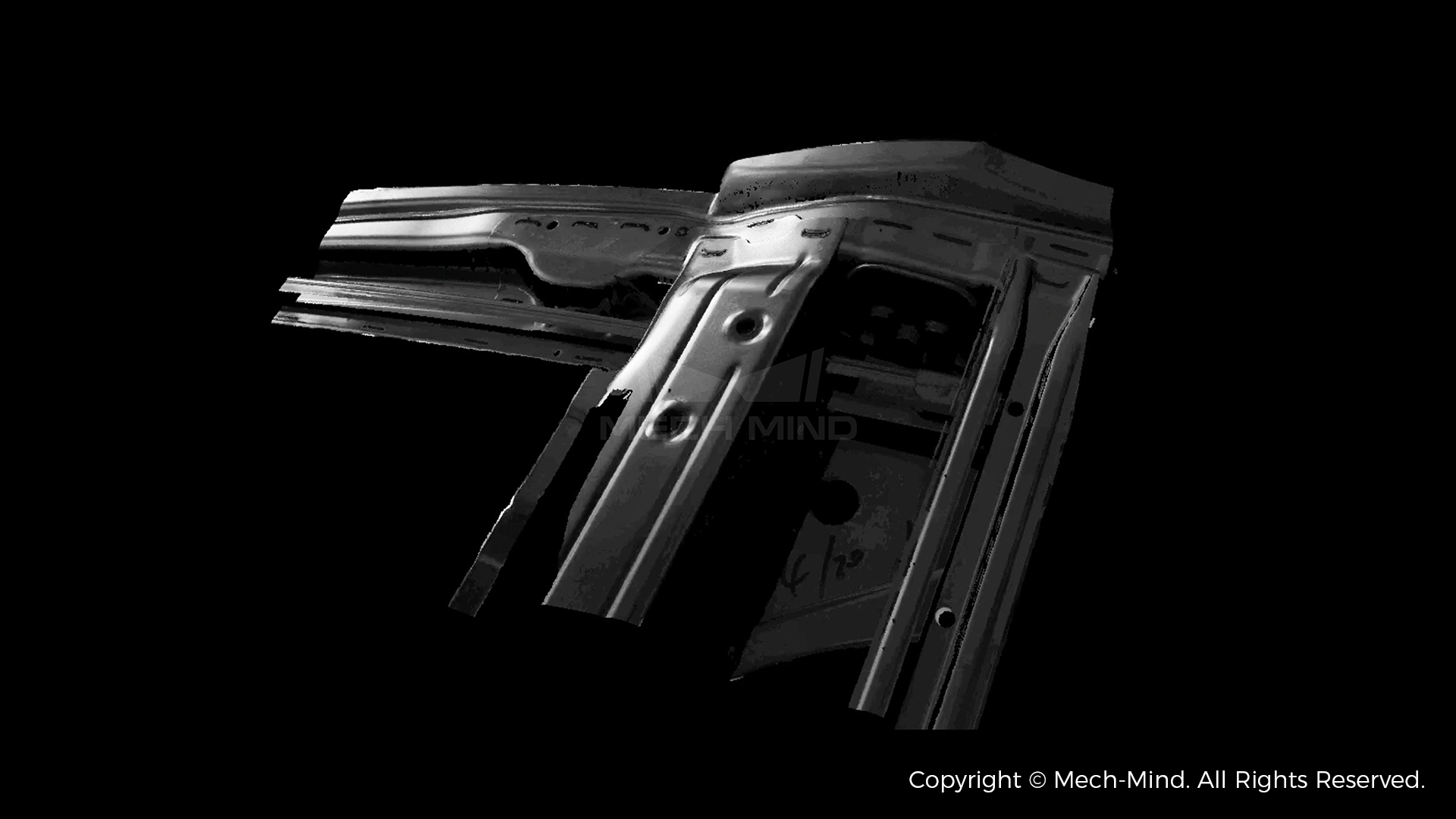
可对反光、型面特征复杂的车身件高质量成像
自研Mech-Vision机器视觉软件内置先进3D视觉算法。获取Mech-Eye采集并生成3D数据后,对工件特征(特征孔、角点、弧线等)进行精准识别定位,计算出机器人抓取位姿。可引导机器人完成支线料箱取放件、主线EMS/料车取件,助力建设无人化焊装流水线。
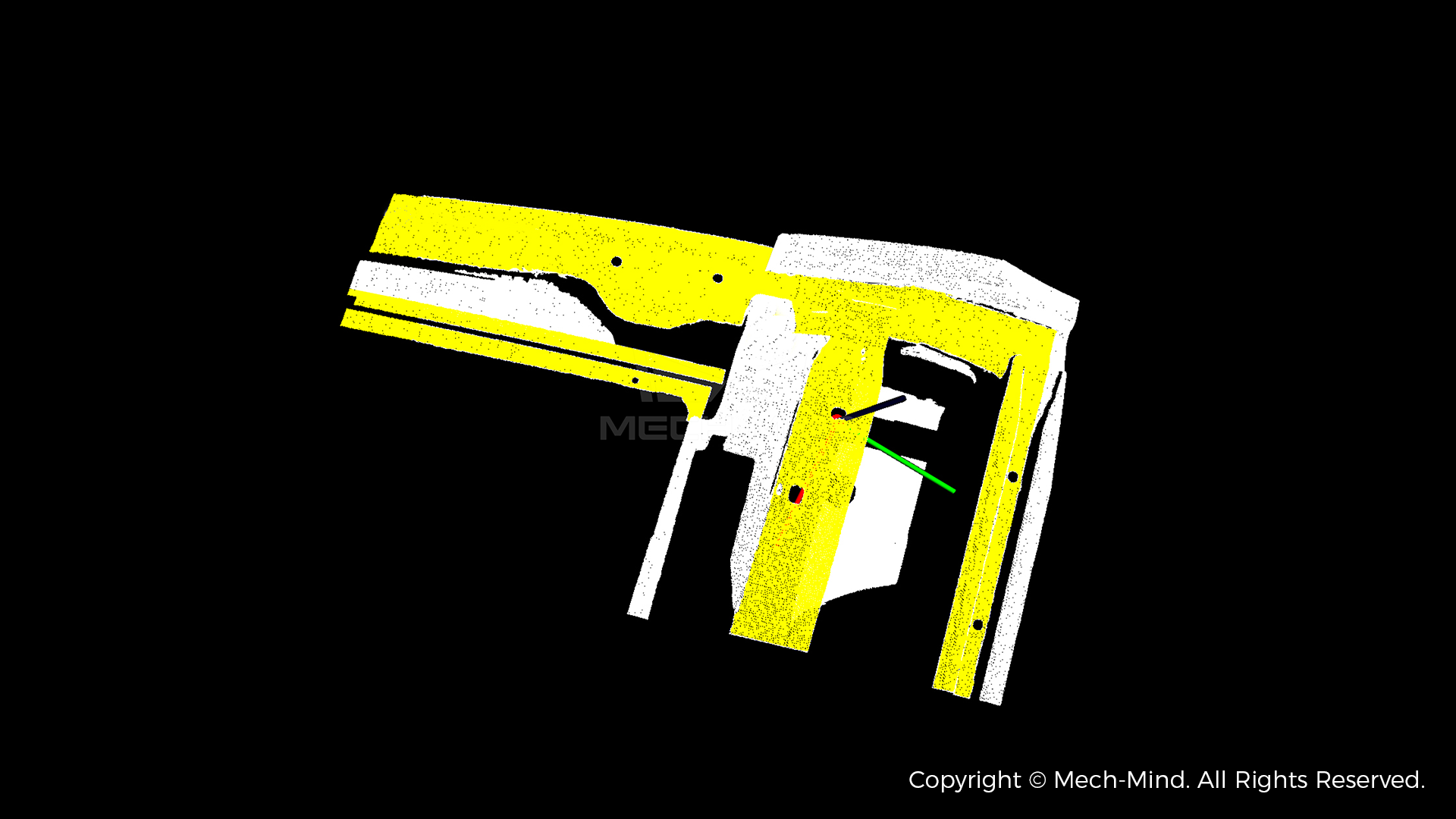
高精度定位工件特征,生成抓取位姿
02 先进AI技术
打造柔性化生产模式
随着消费者对汽车的需求日趋多样化,汽车制造模式已转向“小批量多车型”。采用不限车型不限平台的柔性化混线生产模式能够节约成本、提升效率。并且可以根据市场变化调整生产计划,既保证了汽车生产的规模效益,又满足了市场多元化的需求。
梅卡曼德通过先进的AI技术,使3D视觉系统具备极强的兼容性及通用性,可兼容焊装线体不同车型下的多品类工件。支持自适应夹具切换和导入,缩短夹具更换时间。梅卡曼德以AI技术为主机厂打造出“自适应生产链”,实现了任意车型快速换产,降低新车型导入的改造难度,大大提高生产线柔性度。
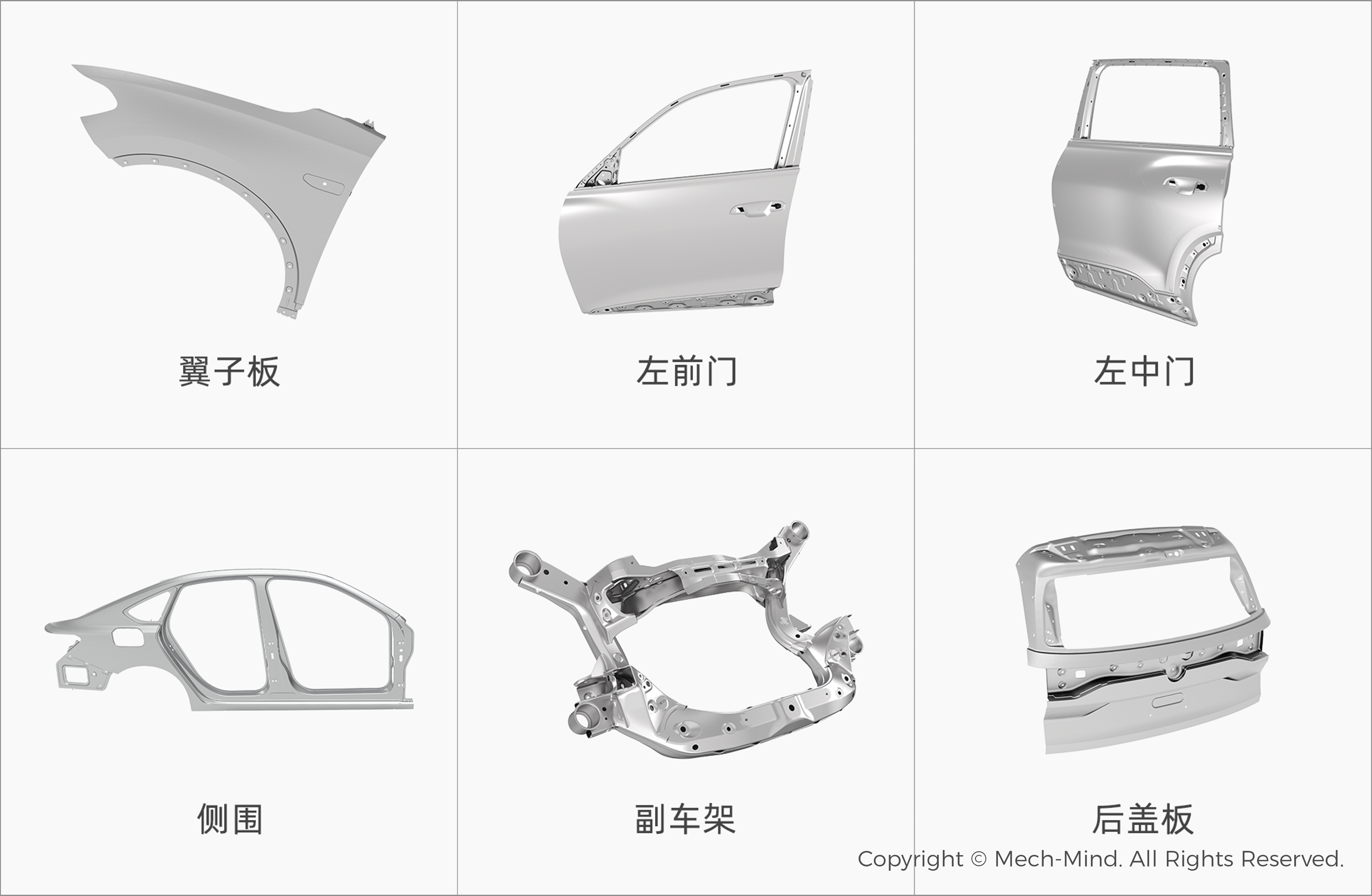
梅卡曼德3D视觉系统可兼容各类工件
在成本控制方面,精盛具、EMS/料车等工装的设计得以大幅简化,优化线体空间利用率,且在长期使用过程中无需再进行精度维护。在解决产线复杂环境光干扰问题上,Mech-Eye工业级3D相机采用了先进的光学技术,在20000lx-30000lx的环境光干扰下也能高质量成像,从而减少了补光、遮光设施的成本投入。
03 稳定可靠
保证产线长期稳定运行
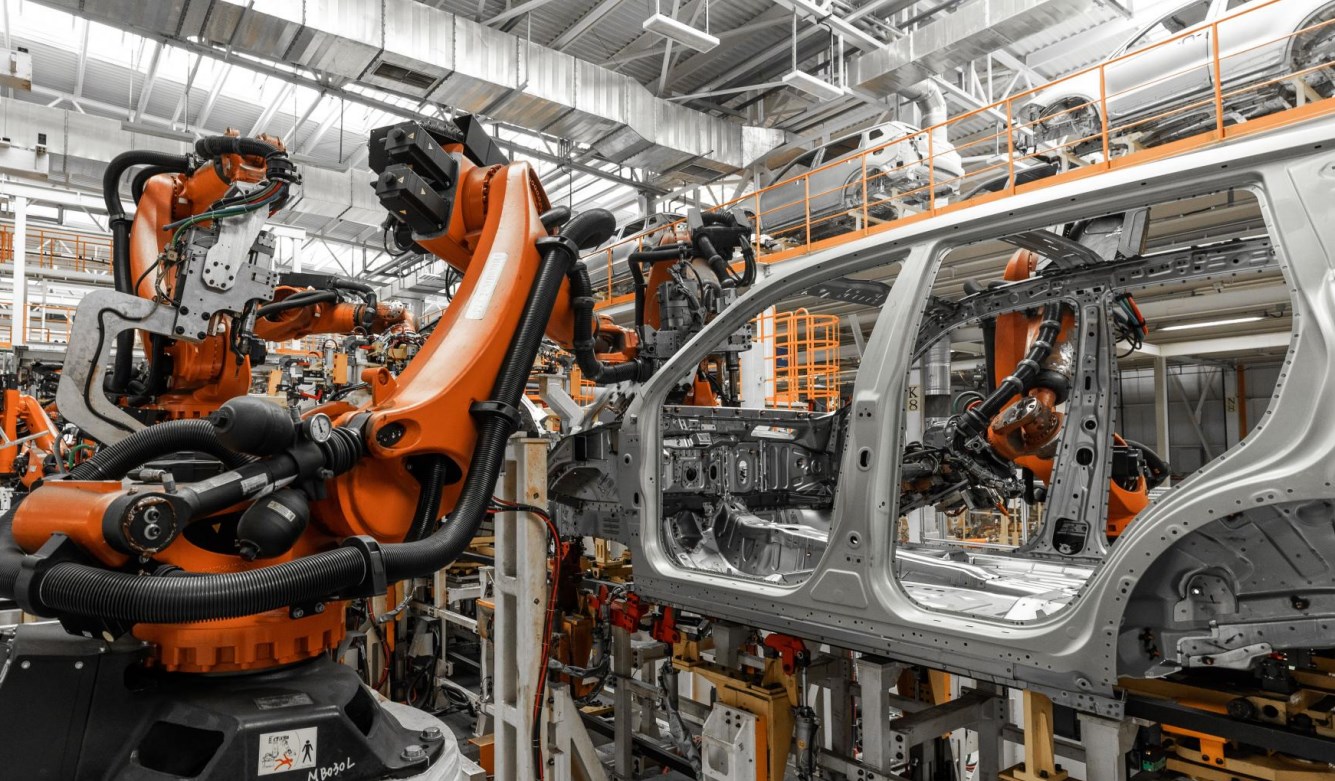
焊装主线白车身拼焊
汽车工厂有着既定的产能目标,多为全自动化流水线,对于设备稳定性要求极高。梅卡曼德旗舰机型均已通过MTBF(平均无故障运行时间,Mean Time Between Failure)≥40000小时认证,相当于连续1666余天无故障稳定运行,可保证客户现场长期稳定运行。
针对系统长期运行带来的误差、系统温漂等问题,梅卡曼德可提供精度补偿功能包,可及时修正系统精度偏移量,并支持精度监控,保证系统精度稳定可靠。也提供快速标定功能包,支持相机更换快速恢复标定,确保产线高效运行。
智能抓取技术能够很好地应对主机厂线体布局紧凑而引起的干涉,快速生成无碰撞的机器人运动路径。视觉系统也支持异常工件报警(形变、尺寸超差等),保证焊合质量。
04 易用性持续升级
快速部署视觉应用
为了帮助集成商伙伴及终端主机厂客户更快速、更便捷地实现视觉功能,我们也对软件易用性不断升级。全新升级的Mech-Vision机器视觉软件整合了通信配置、相机标定、工件识别、路径规划等功能,支持视觉应用的一站式部署。我们也提供样例工程、指导文档、学习地图等资料,新手工程师也能快速完成视觉工程搭建。
各类指导文档及更为简化的视觉工程步骤
应用落地
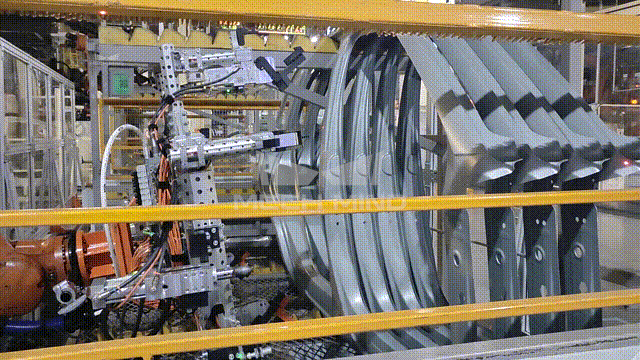
项目现场
此项目终端为国内某知名汽车品牌的制造工厂。在其焊装车间抓件工位,引入了梅卡曼德3D视觉完成侧围外板的高精度插销抓取,实现了多车型柔性切换抓件。工位建设成本及利用率大幅优化,目前已稳定投产。
梅卡曼德致力于以功能强大、简单易用的智能机器人基础设施产品,及交付、培训、市场全链路支持,倾力协助集成商伙伴更快速、便捷地为终端客户交付各类智能机器人应用。
目前,已有众多合资车企和自主车企的焊装自动化线体投入使用了梅卡曼德3D视觉引导抓放件系统,系统精度、稳定性均满足实际需求,工位建设、运维成本大幅降低。